What is Process Improvement? 10 Process Improvement Methodologies
Constant innovation and growth are the new normal for any company that wants to meet customer needs. Organizations have to quickly adjust their strategies and processes and develop new ones to be successful. For this reason, continuous process improvement becomes an integral part of business operations.
Process improvement enables your organization to operate to its full potential, trimming everything that's holding it back, and giving your business tools to boost productivity and growth. It doesn't just eliminate your reoccurring stumbling blocks, but also sets you up for solving new challenges in the future.
In this article, we explain how process improvement helps achieve process excellence and go through the 10 most popular process improvement methods so you can pick which one fits your company best.
What is Process Improvement?
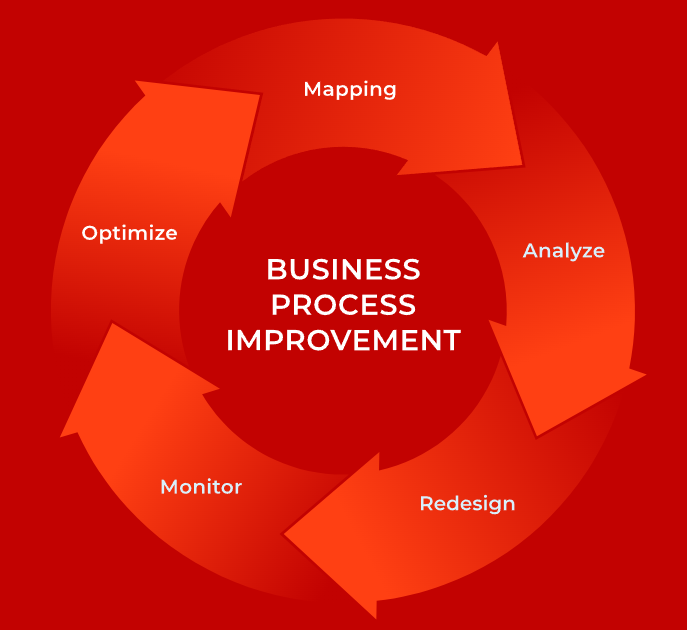
Process improvement is the practice of optimizing existing business processes to meet market standards, improve customer experience, and increase profit. It consists of identifying, analyzing, and improving workflows and is often also referred to as business process management (BPM) or business process improvement (BPI).
The main goals of process improvement are minimizing errors, reducing waste, improving productivity, and streamlining the efficiency of a company's internal and external processes.
Typically, process improvement entails the following activities:
- Evaluating current processes, their effectiveness, and their importance within the company.
- Identifying flawed processes.
- Outlining how improvements would help achieve the business goals.
- Reorganizing available resources (IT, manpower, systems, etc.) for efficient process improvement.
Process improvement goes by various names, including Business Process Management (BPM), Business Process Improvement (BPI), Business Process Re-engineering, and Continual Improvement Process (CIP). Despite the different terms, the objective is the same: to minimize errors, save resources and time, and enhance productivity.
Benefits of Process Improvement
Boost in productivity
When process improvement becomes integral to your organization, all existing processes and workflows are subject to continuous evaluation and enhancement. Such continuous improvement process boosts your efficiency.
Managers can enhance team members’ productivity through better resource allocation, aligning skills with tasks, providing targeted training, and implementing advanced tools and technology. For instance, workflow automation software can help balance workloads, allocate tasks effectively, and automate entire workflows and processes. In addition to that, such software enhances offers real-time visibility and transparency across teams or departments, enabling immediate adjustments and course corrections.
Reduced waste
Reducing waste means eliminating inefficiencies in your processes such as redundant tasks, unnecessary steps, excess resource use, and time delays. Process improvement helps reduce waste by automating workflows, eliminating unnecessary steps, and optimizing resource allocation, leading to more efficient and effective operations.
Eliminating the chance of human error
Logically, incorporating workflow automation in your business processes helps reduce the chance of human errors, but process improvement goes even further. By standardizing procedures and implementing checks and balances, which are the necessary parts of process improvement, you ensure that no mistakes will be left unnoticed and can be fixed right away.
Improved employee satisfaction
By fully embracing process improvement, employees recognize how even small changes can significantly enhance company performance. Automating workflows as part of business process improvement initiatives frees employees from mundane, repetitive tasks, allowing them to focus on higher-value activities. This shift not only makes roles more interesting but also boosts employee engagement and satisfaction. Recognizing contributions with employee recognition software helps foster a supportive environment where employees feel valued, driving greater commitment to process improvement initiatives.
A culture of continuous improvement motivates everyone to perform at their best, leading to higher employee engagement and retention.
Encouraging innovation
By regularly assessing and refining workflows, employees are encouraged to think creatively and propose new solutions. This openness to change and improvement cultivates an environment where innovative ideas are valued and implemented, leading to more efficient and effective operations.
Increased customer satisfaction
Improved business processes result in higher quality products and services, enhancing customer satisfaction and overall experience. For example, a company that implements process improvements in its customer service department might reduce response times and resolve issues more effectively. This leads to happier customers, boosting brand value and driving better financial performance for the company.
Growing profits
As we already mentioned, process improvement helps increase organizations’ efficiency, reduce costs, and enhance product quality. Business process automation allows you to minimize resource use and cut down on errors and delays.
Moreover, improved processes also boost customer satisfaction, leading to higher sales and repeat business, ultimately driving greater profitability.
10 Process Improvement Methodologies You Need to Know
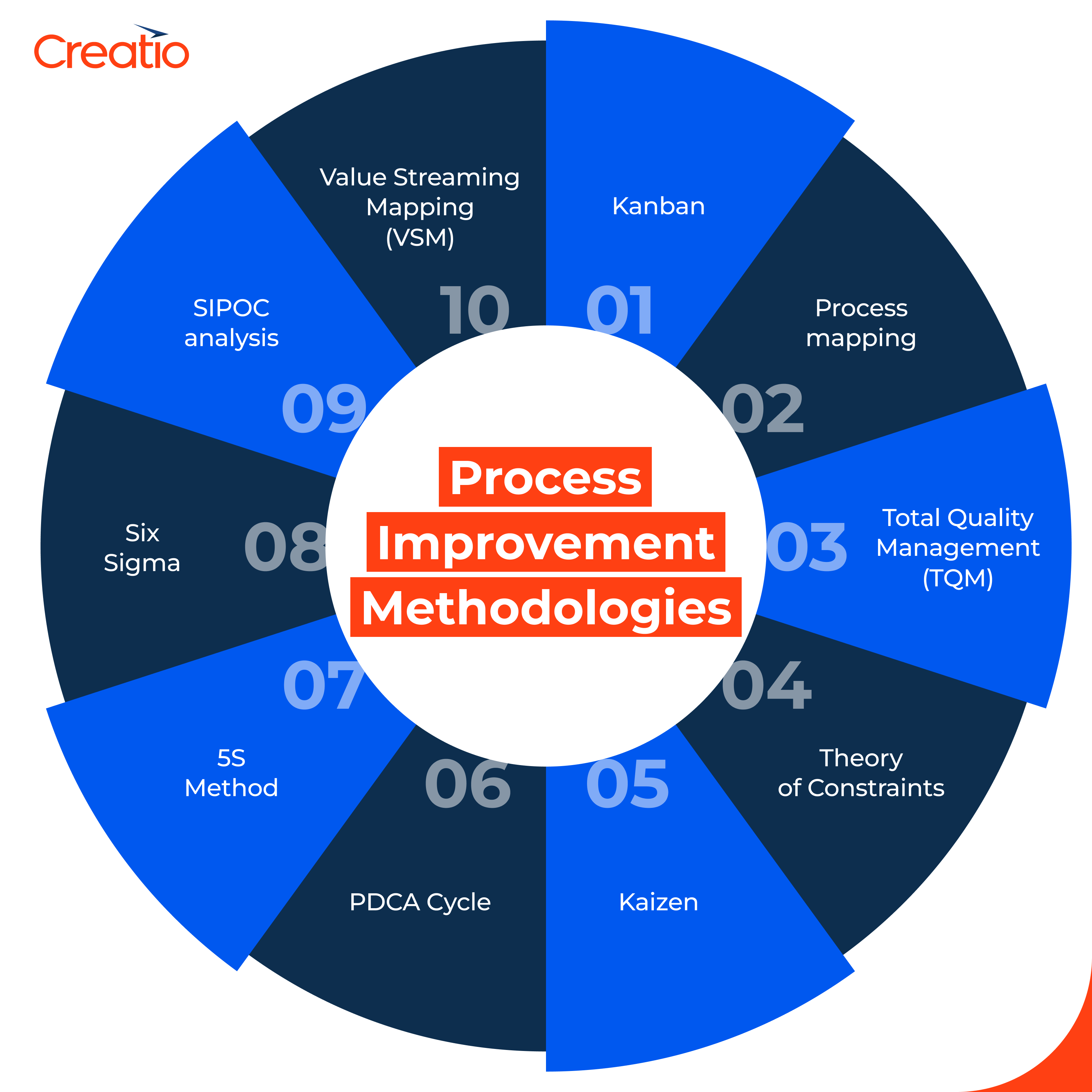
Although they share a common goal, different process improvement methodologies cater to various needs.
Some frameworks emphasize lean techniques to eliminate waste, while others concentrate on fostering a company culture with continuous improvement methodologies. Also, certain process improvement methodologies help companies visually map out their existing processes to see opportunities for increased efficiency and productivity.
In this section, we will go through the ten most popular process improvement methodologies so you can determine which of them suit your needs best.
Kanban
Kanban is a process improvement methodology that uses visual management techniques for continuous process improvement. By visualizing tasks on a Kanban board, teams can easily see the progress of work items, identify bottlenecks, and optimize the flow of tasks from start to finish.
Imagine a software development team using a Kanban board for project management. The board is divided into columns such as "To Do," "In Progress," "Review," and "Done." Each task is represented by a card that moves through these columns as work progresses.
Using Kanban, the team can quickly identify if too many tasks are stuck in the "In Progress" or "Review" stages, signaling a need to address specific issues.
Process mapping
Process mapping is another visualization technique used to illustrate and analyze the steps, activities, and decision points within a specific process. A typical process map outlines process steps, decision points, inputs and outputs, flow sequence, and roles and responsibilities.
By creating a flow diagram, organizations can determine how a process operates, identify areas for improvement, and develop a plan for process optimization.
Total Quality Management
Total Quality Management (TQM) is a comprehensive approach to process improvement that emphasizes continuous enhancement of product and service quality, customer satisfaction, and overall organizational effectiveness. It encourages a culture where every employee is involved in improving processes and outcomes.
The key principles of TQM are:
- Customer focus: understanding and meeting customer needs and expectations. B
- Continuous improvement: an ongoing commitment to identifying opportunities for improvement and making incremental changes to processes.
- Employee involvement: employees are key to achieving quality and process improvements.
- Process-centered approach: focus on understanding and optimizing the entire process rather than just individual tasks or departments.
- Leadership commitment: leaders set the vision, establish clear goals, provide resources, and demonstrate a commitment to quality and continuous improvement.
Theory of Constraints
The Theory of Constraints (ToC) is a process improvement methodology for identifying the most critical limiting factor (constraint) that stands in the way of achieving a goal and then systematically improving that constraint until it is no longer the limiting factor.
This may involve optimizing scheduling, reducing downtime, or improving the efficiency of the bottleneck process. If the constraint cannot be fully exploited with existing resources, the organization may invest in additional capacity or resources to elevate the constraint and increase overall throughput.
Imagine a manufacturing company that produces widgets. The bottleneck in their production process is a specific machine that can only produce a certain number of widgets per hour. Using ToC:
- The company identifies that Machine A is the bottleneck limiting overall production.
- They optimize the machine's operating schedule to maximize its uptime and output, ensuring it operates at full capacity during peak production hours.
- Other parts of the production line are synchronized with Machine A's output to avoid overloading downstream processes and causing unnecessary inventory buildup.
- If demand exceeds the capacity of Machine A, the company may consider investing in a higher-capacity machine.
ToC advocates for a continuous improvement cycle where the focus shifts to the next constraint once the current one is addressed. This iterative process helps organizations steadily improve performance and achieve their strategic goals.
Kaizen
Kaizen is a process improvement methodology that emphasizes continuous, incremental improvements in all aspects of an organization. Rooted in Japanese management practices, Kaizen combines lean and agile principles to enhance quality and productivity by making small, ongoing changes. The core idea is that small, consistent improvements add up to significant long-term gains.
Let's take the manufacturing company from the previous example and see how Kaizen methodology could improve its operations. Workers on the assembly line would be encouraged to identify inefficiencies or potential improvements in their daily tasks. For instance, an employee could notice that reaching for tools repeatedly slows down the process.
Then, the team implements a small change by rearranging the tool placement, making them more accessible to reduce the time spent reaching for them. The improvement is monitored, and feedback is collected from employees to ensure it has a positive impact.
The change is then standardized if it proves effective, and employees are encouraged to continue identifying other areas for improvement.
PDCA Cycle
PDCA is part of the Kaizen methodology and stands for plan, do, check, and act. It helps companies identify the issues, create, and implement solutions, evaluate data, and document the final results to implement the plan.
5S Method
The 5S technique is a foundational component of both Kaizen and Lean methodologies, focusing on workplace organization and standardization to improve efficiency and productivity. The name 5S describes the five steps of the process, which are:
- Sort: Remove unnecessary items from the workspace. This step involves evaluating tools, materials, and equipment, and eliminating anything that is not needed for current operations.
- Straighten: Arrange necessary items in an orderly manner so they can be easily accessed and used. This step focuses on organizing tools and materials in a way that minimizes wasted time and effort.
- Shine: Maintain the organization established at the previous steps. Regular cleaning and maintenance help to identify and address issues such as leaks, malfunctions, or wear and tear. A clean environment promotes safety and efficiency.
- Standardize: Establish standardized procedures and practices to maintain the first three steps. This involves creating guidelines and schedules for sorting and organizing, and cleaning, ensuring that these practices are consistently followed.
- Sustain: Make 5S a habit and a part of the organizational culture. This step requires ongoing training, communication, and commitment from all employees to maintain and continuously improve the standards set in the previous steps.
Six Sigma
Six Sigma stands for pulling workers up through ranks by the principle of karate belts. A person starts as a green belt and goes to the black belt. Six Sigma involves two ways and several steps to get there: define, measure, analyze, improve and control (DMAIC) and define, measure, analyze, design, and verify (DMADV).
Let's go back to our example of a manufacturing company. Imagine there are high defect rates in one of its product lines. The company could use the DMAIC framework to address the issue:
- Define: The team defines the problem as a high defect rate in the production of a specific component, setting a goal to reduce defects by 50% within six months.
- Measure: Data is collected on the current defect rates, production processes, and contributing factors, establishing a baseline for comparison.
- Analyze: The team analyzes the data to identify root causes of the defects, such as variations in material quality or inconsistencies in machine settings.
- Improve: Solutions are developed and implemented, such as standardizing machine settings, improving material inspection processes, and providing additional training for operators.
- Control: Control mechanisms, such as regular audits and monitoring systems, are put in place to ensure the improvements are maintained and the defect rates remain low.
SIPOC analysis
SIPOC analysis is a valuable tool used within the Six Sigma methodology, particularly during the Measure phase of DMAIC (Define, Measure, Analyze, Improve, Control) or DMADV (Define, Measure, Analyze, Design, Verify) frameworks. SIPOC stands for Suppliers, Inputs, Process, Outputs, and Customers. It provides a high-level overview of a process and helps to clarify key elements before diving into process improvements.
Value Stream Mapping
Value stream mapping is a lean-management technology that helps to analyze the current state and design a future development strategy for the processes. VSM displays all critical steps in a specific process and quantifies the time and volume taken at each stage. It can be constructed with the help of special software or in Excel and Word formats.
Examples of Process Improvement
Process improvement methodologies can enhance any business area. For that reason, there can be countless examples of a process improvement methodology in action. Here are some of them:
- Automating repetitive tasks
- Eliminating unnecessary tasks
- Reducing excessive and insecure email communication
- Adding approval steps to ensure service or product quality
- Replacing approval steps by notifications for well-functioning processes
- Incorporating conditions into automated processes to handle exceptions
- Automating data input to minimize manual entry
- Hiding irrelevant fields in questionnaires for certain participants
- Integrating processes with other software for tasks like creating folders, updating spreadsheets, scheduling events, and adding journal entries automatically
5 Tips for Process Improvement Implementation
1. Limit your area of focus
To avoid feeling overwhelmed, limit the number of improvement initiatives and begin with smaller projects. Focus on high-priority areas that need immediate attention, such as a single workflow or process.
2. Create a plan
Without a clear plan, process improvements can be poorly implemented and ineffective. Ensure each initiative has a documented plan with due dates, deliverables, roles, and accountability.
3. Choose the right technology
Choose tools that fit your needs for tracking and managing improvements. No-code automation solutions with visual interfaces simplify creating and optimizing workflows. Look for software that integrates with your existing systems for better control and visibility.
4. Standardize
Document and share improvements, then establish standards and procedures to manage them properly. Update these standards as improvements are made and inform everyone involved of the changes.
5. Automate
Automate recurring tasks to improve process efficiency. Automation standardizes tasks, consolidates data, eliminates communication silos, and enhances accuracy and speed by reducing manual work and routing items through workflows using predefined rules.
How Creatio's No-Code Platform Accelerate Process Improvement
Automation is key to process improvement since it eliminates manual work and helps you save resources. As we mentioned above, a large part of process improvements depends on choosing the right tools.
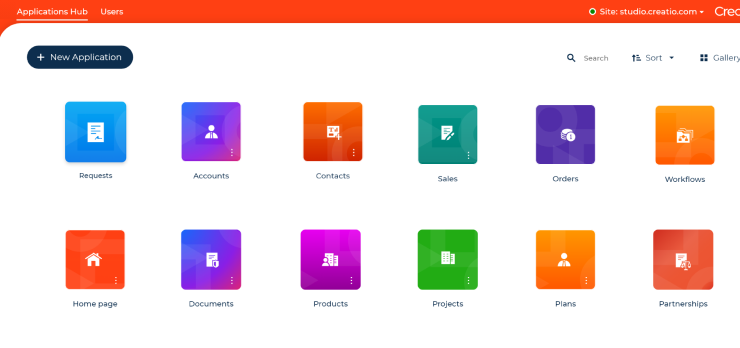
Creatio stands out as the best workflow automation platform, empowering organizations optimize their workflows with a maximum degree of freedom, thanks to its no-code capabilities, composable architecture, and generative AI tools.
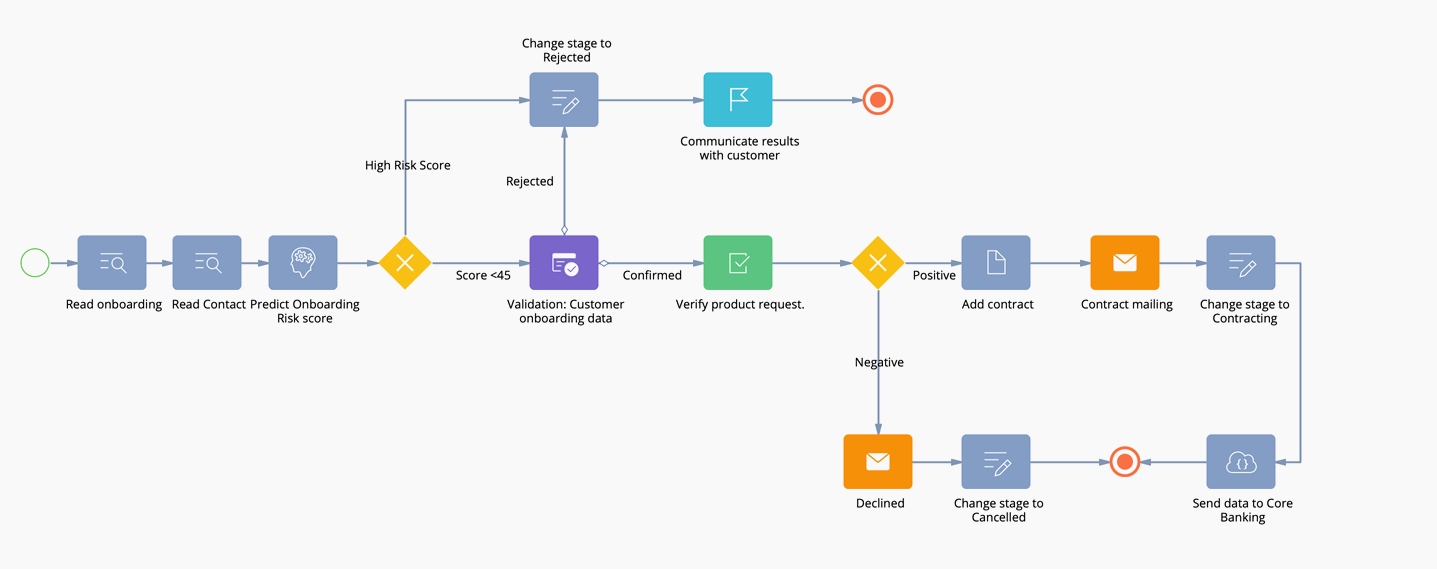
An example of workflow automation in Creatio
Creatio's composable architecture allows you to build your own automated workflows without any need for software development skills. You can use Creatio's visual interface and functional blocks and components to build new automated processes with drag-and-drop tools.
Additionally, Creatio's generative AI features can help you create new workflows by recommending necessary components or customizing out-of-the-box features. Creatio.ai, a generative AI assistant, can even create new business apps based on the requests made in natural language.
For example, you can tell it to create a new workflow that helps process and approve contracts, and it will offer a prototype to you in a matter of seconds with no effort spent on your part.
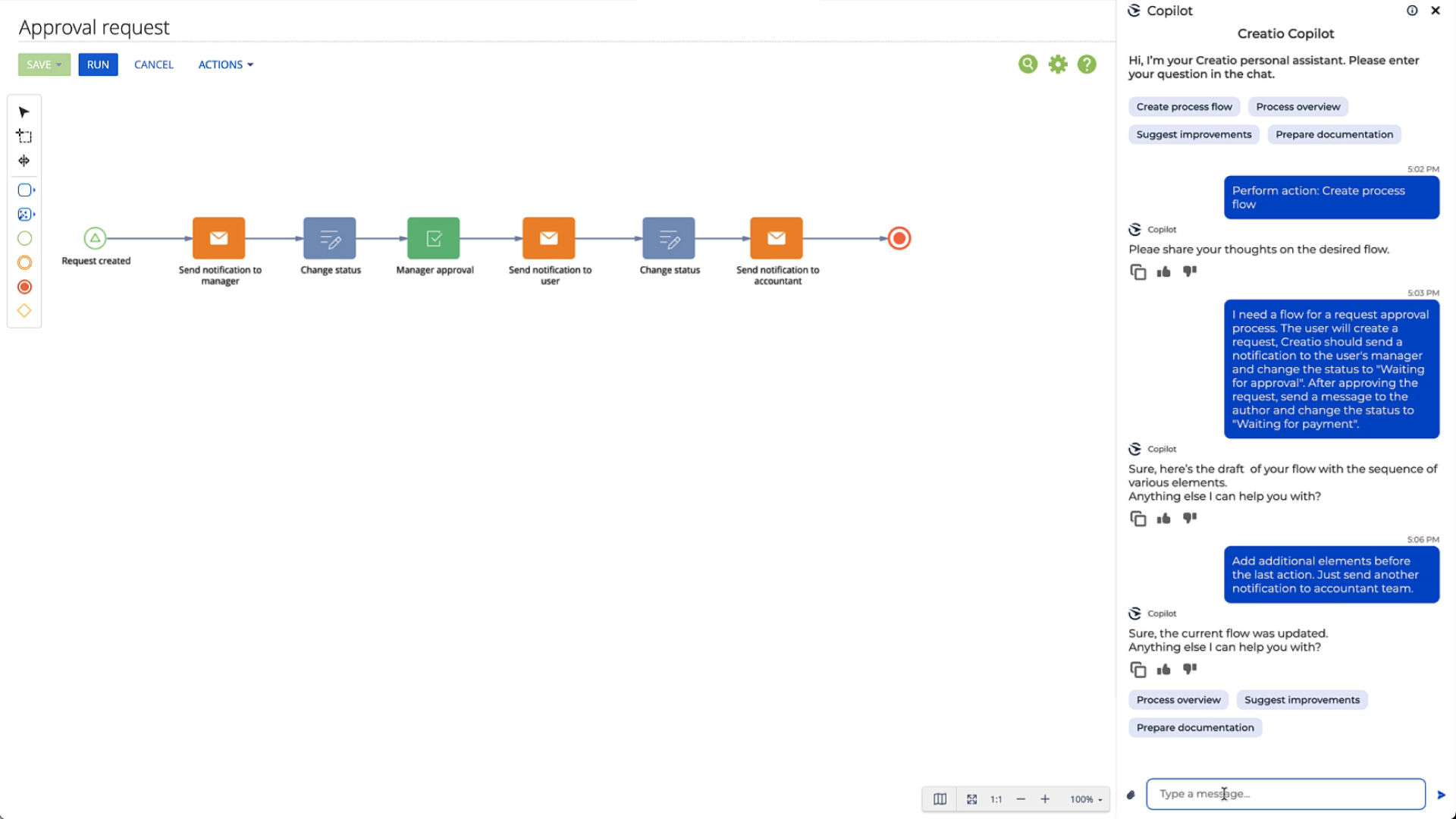
Creatio.ai scenario
Creatio's robust analytics and reporting capabilities provide valuable insights into process performance, allowing organizations to track key metrics, identify trends, and make data-driven decisions to optimize their operations. This real-time visibility helps managers monitor progress, identify bottlenecks, and address issues as they arise.
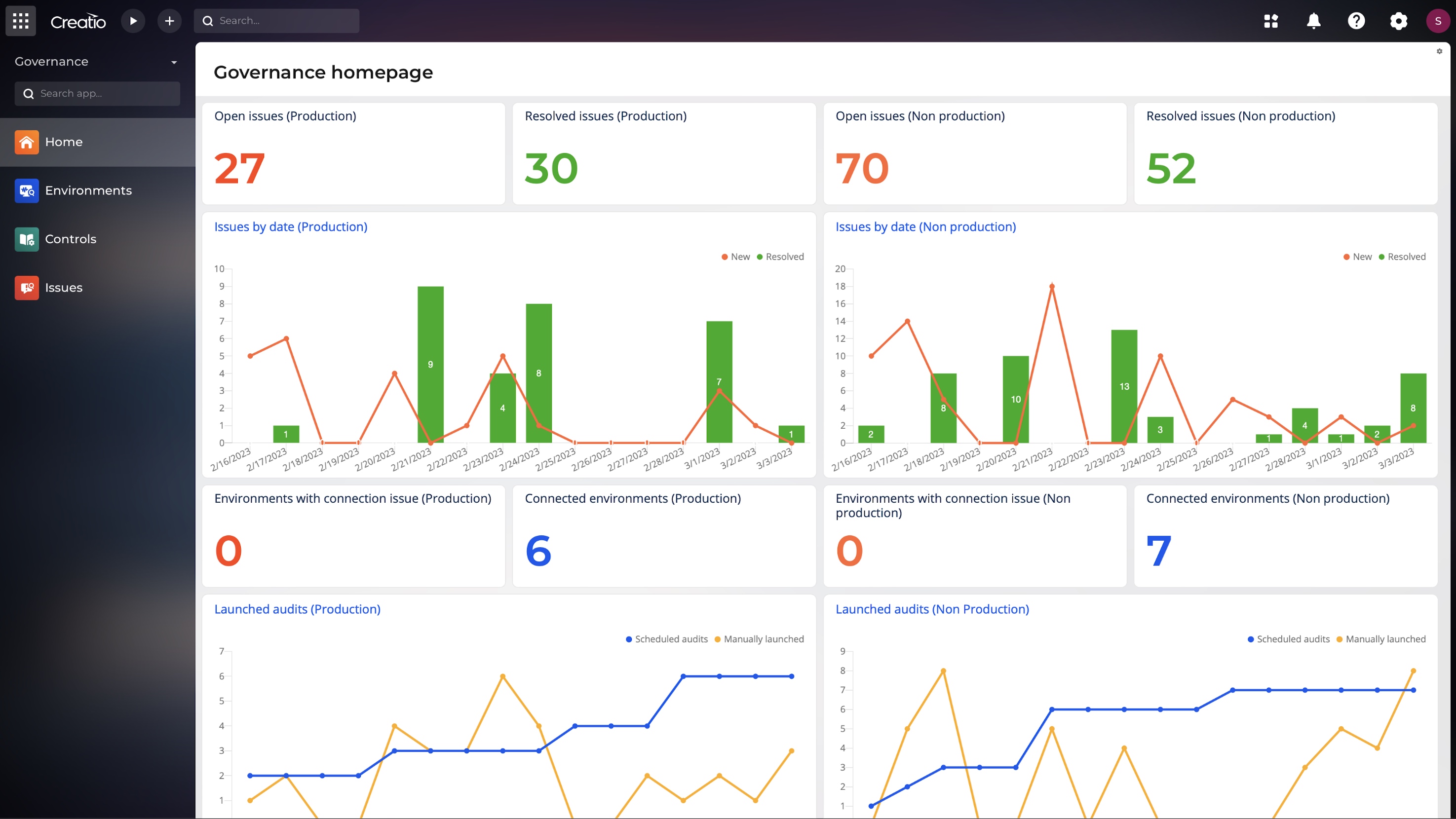
Creatio's governance dashboard
Creatio offers a powerful combination of business process management functionality, automation, analytics, and flexibility, making it the ideal tool for organizations looking to enhance their process excellence initiatives. Sign up for Creatio's free trial to experience the freedom of automation yourself!