What is Process Excellence? A Comprehensive Guide
In the ever-evolving landscape of contemporary commerce, organisations are compelled to seek avenues for securing a competitive advantage and enhancing their operational efficacy to remain at the forefront. To operate with greater efficiency, elevate productivity, and surpass customer anticipations, enterprises are increasingly adopting the principles of process excellence.
In this article, we shall delve into the foundational principles of process excellence, elucidate its benefits, and delineate strategies that organisations can employ, demonstrating how entities can strategically harness these methodologies to refine their business processes and attain enduring success.
What is Process Excellence?
Process excellence pertains to the application of superior practices and advanced tools in business process management and workflow automation aimed at enhancing the effectiveness and efficiency of an organisation’s varied operations. It encompasses the rigorous and continuous evaluation of current processes to highlight opportunities for refinement, eliminate inefficiencies, and foster seamless integration across disparate business functions.
By adopting the principles of process excellence, organisations can optimise their operations, leading to enhanced productivity, reduced operational costs, accelerated decision-making, and sustained growth. This disciplined approach enables businesses to achieve higher standards of operational performance and agility.
What factors determine process excellence?
Process excellence is influenced by a variety of factors that may differ depending on the business’s specific nature and operational context.
A process is deemed excellent when it satisfies the following criteria:
- Efficiency
- Accuracy
- Quality
- Measurability
- Innovation
- Agility
- Flexibility
- Adaptivity
- Security
- Compliance
In addition to meeting these criteria, an exemplary process should also:
- Align with business strategy
- Improve productivity
- Boost customer satisfaction
- Reduce costs
- Achieve business goals
By employing these criteria, organisations can evaluate and refine their processes to achieve excellence. A process should be continually optimised until it satisfies all relevant criteria or those specifically determined by the organisation.
Benefits of Business Process Excellence
The pursuit of process excellence offers myriad advantages to organisations across a spectrum of industries. Among the principal benefits are:
- Augmented efficiency: Streamlining organisational processes reduces waste, mitigates errors, and ensures smoother operations, thereby elevating overall productivity and operational efficiency.
- Enhanced productivity: By optimising workflows, process excellence enables employees to execute tasks with great swiftness and effectiveness, thus substantially boosting output.
- Superior quality: The standardisation of procedures coupled with rigorous quality control measures allow organisations to deliver products and services of elevated calibre.
- Elevated customer satisfaction: Process excellence ensures that customer needs are addressed with promptness and precision, fostering heightened satisfaction and bolstering customer loyalty.
- Cost reduction: The identification and eradication of inefficiencies facilitate significant savings on resources, labour, and other expenditures, thereby enhancing profitability.
- Accelerated time-to-market: Efficient processes enable organisations to introduce products and services to the market expeditiously, conferring a competitive advantage and allowing for swift adaptation to emerging trends and opportunities.
- Augmented agility: The adaptability and flexibility of refined processes empower organisations to respond swiftly to shifting market conditions, evolving customer preferences, and regulatory demands.
- Improved employee experience: Engaging employees in process excellence initiatives fosters their active contribution to organisational success, enhancing engagement and job satisfaction.
- Strengthened competitive position: By consistently delivering superior products and services, organisations can differentiate themselves from rivals and sustain a robust market presence.
- Sustainable growth: Process excellence established a foundation for enduring success by cultivating a culture of innovation and continuous improvement, thereby securing long-term growth.
Essential stages to Achieve Process Excellence
Attaining process excellence necessitates a meticulous approach and a steadfast dedication to ongoing refinement. Organisations aspiring to this level of operational prowess should follow these pivotal stages:
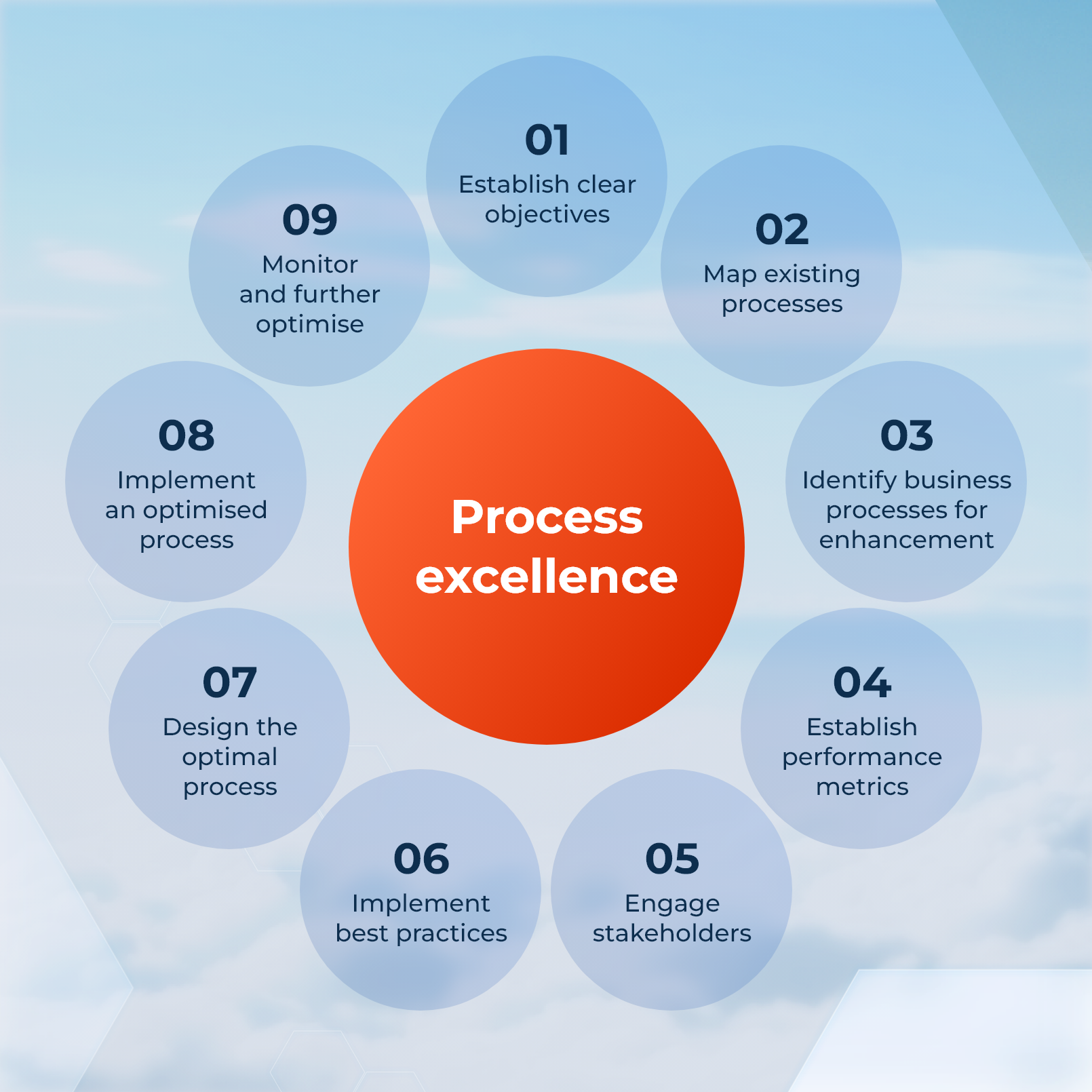
1. Establish clear objectives
Begin by setting forth precise objectives for process excellence endeavours, ensuring they are aligned with the organisation's strategic ambitions and priorities. It is crucial to determine the criteria for process excellence to enable accurate assessment of the effectiveness of process modifications.
2. Map existing processes
Conduct a thorough examination of current processes to identify the specific steps, resources, and objectives of each operation within your organisation. Utilise process mapping tools to elucidate and comprehend the existing state with greater clarity, thus facilitating a more informed approach to improvement.
3. Identify business processes for enhancement
Ascertain which processes should be improved, pinpointing opportunities to augment efficiency and curtail costs. The objective is to develop optimised iterations of each operational procedure within the organisation. However, to achieve success, it is imperative to concentrate on refining one process at a time.
4. Establish performance metrics
Define key performance indicators (KPIs) to gauge the efficacy and efficiency of the processes. These metrics should be specific, measurable, achievable, relevant, and time-bound (SMART) to ensure precise tracking of progress. It is essential to evaluate the current performance of processes meticulously to facilitate a robust comparison following the implementation of process excellence enhancements.
5. Engage stakeholders
Involve employees, managers, and other pertinent stakeholders in the process of excellence improvements. Foster an environment of open communication, collaboration, and constructive feedback to garner support and ensure the engagement of all relevant parties.
6. Implement best practices
Conduct comprehensive research into industry best practices and benchmarks to identify methodologies for optimising processes. Employ established and reputable frameworks such as Six Sigma, Total Quality Management (TQM), or Business Process Reengineering (BPR) where appropriate. In subsequent sections of this article, we shall explore these process excellence techniques in greater detail.
7. Design the optimal process
The design of the ideal process entails crafting an optimal workflow that maximises operational efficiency, minimises waste, and ensures the delivery of superior results. This stage is paramount for achieving business process excellence, as it provides the blueprint for the execution of work henceforth.
Here is how your organisation might approach this stage:
- Envision the optimal state of the process, integrating best practices, industry standards, and stakeholder requirements. Carefully document the proposed workflow from inception to completion.
- Scrutinise each step of the process to identify opportunities for streamlining and simplification through advanced process mapping techniques. Eliminate superfluous tasks, redundancies, and impediments that obstruct progress.
- Determine the most effective allocation of resources, including personnel, time, and materials, to underpin the efficient execution of the process. Factor in considerations such as workload, skill requirements, and resource availability to ensure operational smoothness.
- Establish standardised procedures and guidelines for the execution of each task within the process. Diligently define roles, responsibilities, and decision-making authority to foster uniformity and accountability.
- Ascertain opportunities for automation to refine repetitive tasks, diminish manual errors, and accelerate processing times. Utilise advanced technological solutions such as workflow automation software, to mechanise routine activities.
- Architect the process to be both flexible and adaptable, accommodating evolving circumstances, requirements, and priorities.
- Ensure that the meticulously designed process adheres to applicable regulations, industry standards, and internal policies. Integrate necessary checks and controls to mitigate risks and sustain regulatory compliance throughout the entire lifecycle of the process.
- Pilot the new process on a constrained scale to assess its efficacy and uncover any potential issues or areas for enhancement prior to a comprehensive rollout.
- Thoroughly document the designed process, encompassing detailed procedures, workflows, roles, and responsibilities.
8. Implement an optimised process
Execute the enhancements to the processes and furnish extensive training and support to all stakeholders to guarantee their comprehension of the newly devised process, including roles, responsibilities, and any revised procedures.
9. Monitor and further optimise
Post-implementation, it is imperative to engage in continuous scrutiny to perpetually assess the performance of the newly established processes. Utilise predefined KPIs to gauge its effectiveness, identify potential areas for refinement, and effectuate necessary adjustments.
Implementing a perpetual improvement cycle is essential to ensure that the process remains aligned with organisational objectives and contributes to securing a competitive advantage.
Tools and Techniques for Process Excellence
In this section, we shall delve into a range of tools and techniques that organisations can utilise to attain process excellence. From Kaizen to the 5s methodology, myriad approaches are available to assist in optimising processes and refining operations:
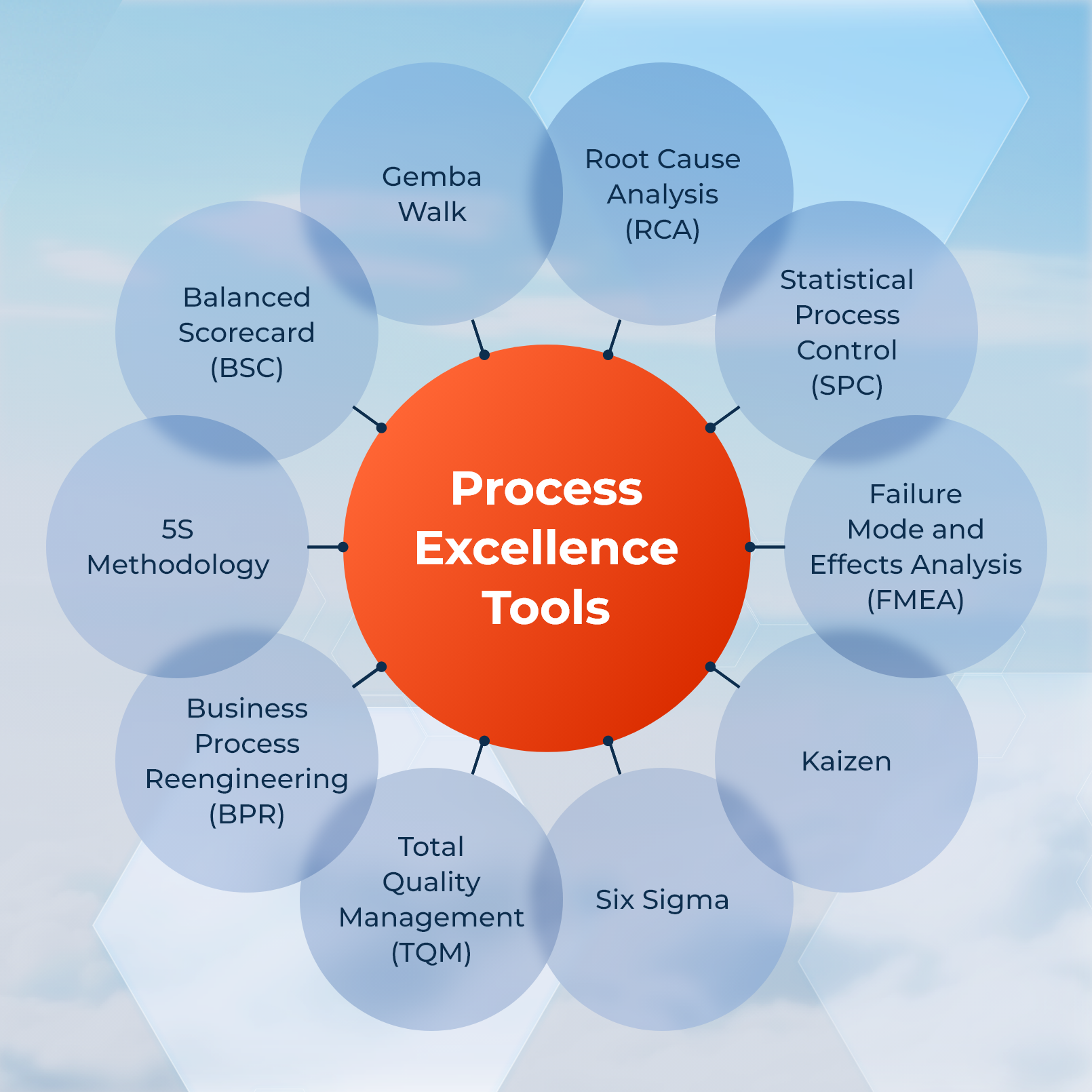
- Root Cause Analysis (RCA): A diagnostic technique employed to ascertain the fundamental causes of issues or deficiencies within a process. By probing deeply into the root causes, organisations can uncover actionable solutions and address the underlying problems with efficacy.
- Statistical Process Control (SPC): A quality control approach that leverages statistical methods to oversee and regulate the consistency and performance of a process. This technique involves the collection and analysis of data over time to detect variations, thus identifying opportunities for enhancement and ensuring process stability.
- Failure Mode and Effects Analysis (FMEA): A rigorous process excellence methodology employed to systematically identify and prioritise potential failures within a process, along with their possible effects and root causes. This approach aids organisations in mitigating risks by proactively addressing potential issues before they manifest.
- Kaizen: Originating from the Japanese term meaning "continuous improvement", Kaizen is both a philosophy and methodology dedicated to effecting small, incremental enhancements to processes over time. It underscores the importance of employee engagement, collaborative teamwork, and fostering a culture of perpetual learning.
- Six Sigma: A data-driven methodology designed to elevate process quality by minimising variability and imperfections to achieve near-perfect performance. It adopts a structured framework encompassing the define, measure, analyse, improve, and control (DMAIC) phases, or define, measure, analyse, design, and verify (DMADV) phases, to pinpoint and eradicate sources of variation.
- Total Quality Management (TQM): A comprehensive management approach centred on the relentless pursuit of quality enhancement across all aspects of an organisation. TQM places a premium on customer satisfaction, active employee participation, and the utilisation of a variety of tools and techniques to elevate processes, products, and services.
- Business Process Reengineering (BPR): An approach entailing the fundamental business redesign and restructuring of core business processes to effectuate substantial gains in performance, efficiency, and competitiveness. BPR compels organisations to reassess and radically overhaul their processes, frequently leveraging technological advancements and innovative practices to achieve transformative outcomes.
- 5S Methodology: A systematic methodology to workplace organisation that originated in Japan, aimed at cultivating a safe and efficient work environment. The five S's - sort, set in order, shine, standardise, and sustain - are employed to drive process excellence by eliminating inefficiencies, enhancing productivity, and fostering a culture of continuous improvement.
- Balanced Scorecard (BSC): A strategic management framework designed to translate an organisation's mission and strategy into a holistic set of performance metrics encompassing four distinct perspectives: financial, customer, internal processes, and learning and growth.
- Gemba Walk: A lean management practice wherein managers visit the actual site of operations to observe processes firsthand, identify areas for enhancement, and engage directly with employees. This practice fosters direct observation and dialogue at the operational source, facilitating the attainment of process excellence.
Guidance for Attaining Process Excellence
A multitude of pragmatic strategies can assist organisations in the pursuit of process excellence. By prioritising customer value, fostering collaboration, and enhancing communication, we have identified five hey tip that provide actionable insights for enhancing efficiency:
1. Prioritise customer value
Anchor your process excellence initiatives in the consistent delivery of value to customers. Gain a deep understanding of the needs, preferences, and challenges of your target audience, and tailor processes to meet these demands. Strive to provide a personalised experience and exceptional service to cultivate lasting customer loyalty.
2. Monitor and evaluate outcomes
Vigilantly monitor and measure the outcomes of newly implemented processes. Regularly access key performance indicators, such as cycle time, error rates, customer satisfaction scores, and cost savings, to evaluate the effectiveness of process enhancements.
By maintaining a close watch on these metrics, organisations can ensure that process changes deliver the desired results, empowering them to make informed, data-driven decisions to ongoing improvement.
3. Emphasise perpetual improvement
Cultivate a culture of continuous improvement as a cornerstone of business process excellence. Regularly implement small, incremental changes to progressively enhance processes over time.
Foster an environment that encourages experimentation, embraces the lessons learned from failures, and adapts to the evolving circumstances within your organisation to sustain ongoing progress.
4. Maintain agility
In the ever-accelerating realm of modern business, agility is paramount to success. Adopt a flexible and adaptable approach to process excellence, enabling your organisation to swiftly navigate changing market conditions, stay abreast of the latest industry trends, and adeptly respond to emerging opportunities, and evolving customer needs.
5. Invest in process management tools
Allocate resources to a Business Process Management (BPM) platform to refine process design, execution, monitoring, and optimisation. A BPM platform provides a centralised repository for documenting business processes, capturing data, and automating workflows, thereby enhancing collaboration and visibility across the organisation.
With capabilities such as process modelling, workflow automation, analytics, and reporting, a BPM platform empowers organisations to standardise processes and elevate productivity.
By adhering to these principles, organisations can cultivate a culture of process excellence, enabling them to attain operational efficiency, superior quality, and elevated customer satisfaction, all while promoting innovation and constant improvement.
Process Excellence vs. Operational Excellence vs. Business Excellence
In this section, we shall delineate the distinctions between Process Excellence (PEX), Operational Excellence (OpEX), and Business Excellence (BEX). Although these concepts converge on the common objective of realising organisational success, they differ in scope and methodology:
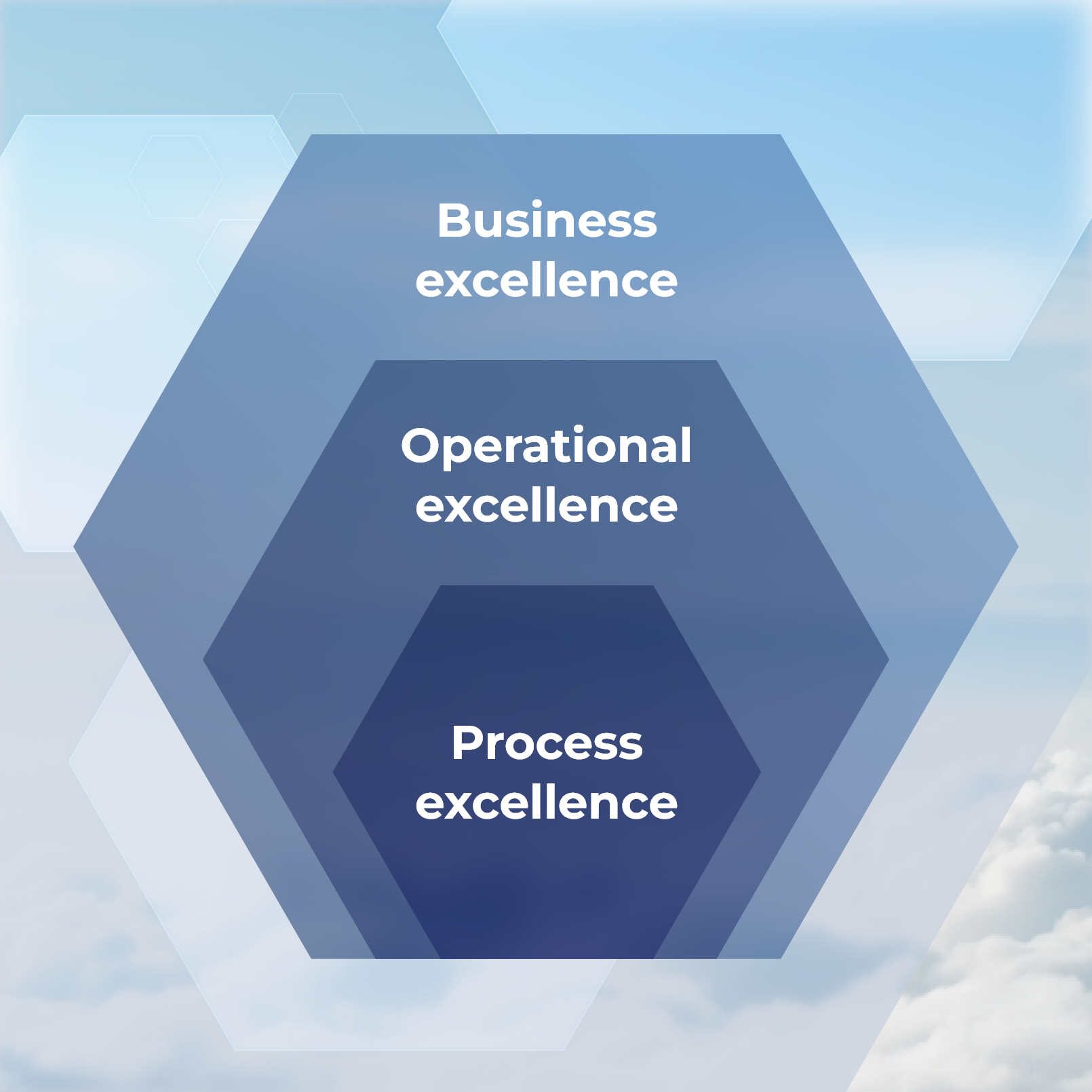
Process Excellence (PEX)
Process Excellence is a methodical approach centred on the identification, analysis, and optimisation of processes within an organisation, with the aim of enhancing efficiency, quality, and overall performance.
It concentrates on refining workflows, eliminating waste, and nurturing a culture of continuous improvement to drive organisational success.
Operational Excellence (OpEX)
Operational Excellence represents a more expansive concept, encompassing not merely process improvement but also the alignment of every facet of an organisation's operations with its strategic objectives. It involves optimisation of people, processes, and technology to achieve superior operational efficiency, profitability, and a sustainable competitive advantage.
Business Excellence (BEX)
Business Excellence embodies the zenith of organisational performance, transcending mere operational efficiency to encompass innovation and stakeholder satisfaction. BEX extends beyond the optimisation of processes and operations, emphasising comprehensive business management practices that underpin sustained success.
This concept involves attaining excellence across various dimensions, including leadership, strategy, customer focus, workforce engagement, and social responsibility. In doing so, it positions the organisation as an industry leader and a paragon of excellence for others to emulate.
Elevate Your Process Excellence with Creatio
In the pursuit of process excellence, the availability of the appropriate tools can prove transformative. Creatio distinguishes itself as a premier BPM platform, empowering organisations to streamline their operations and optimise workflows with unparalleled flexibility, thanks to no-code capabilities and composable architecture.
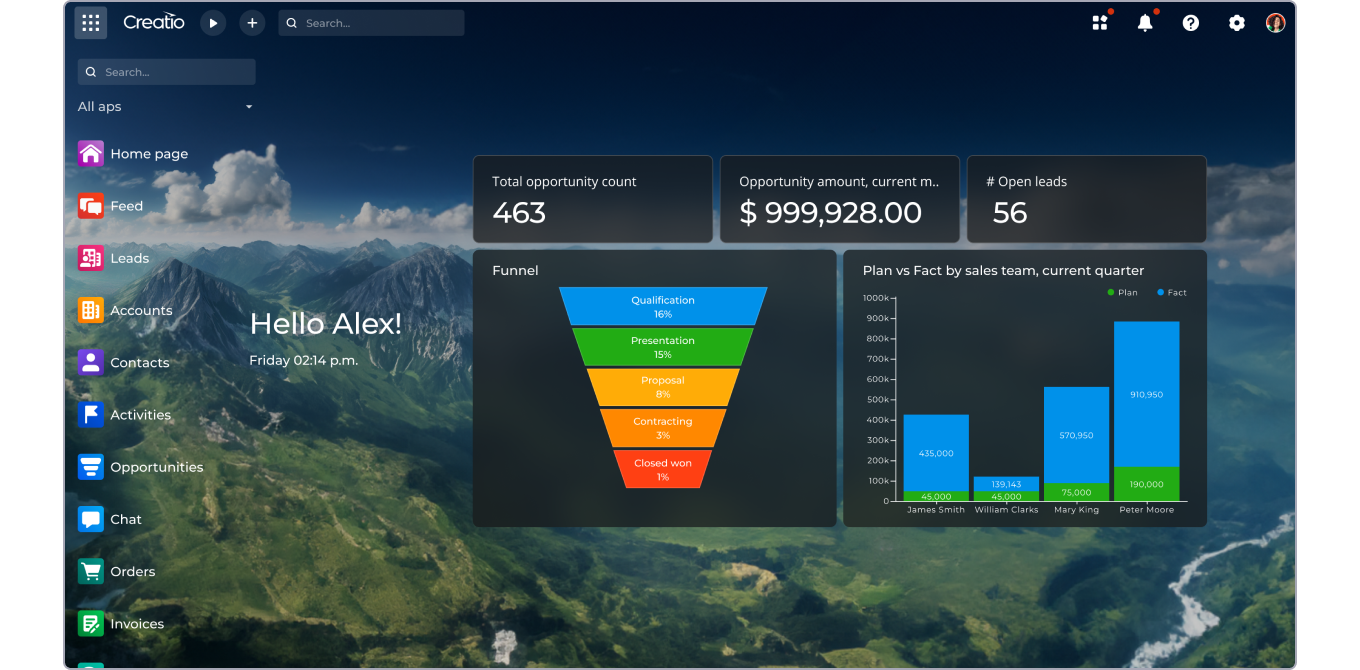
Creatio offers an extensive suite of tools and features designed to support every phase of the process lifecycle, from design and automation to monitoring and analysis. Its intuitive process modelling capabilities allow users to visually map their processes, identify inefficiencies, and craft optimised workflows tailored to their specific requirements.
Through Creatio's business process automation capabilities, organisations can automate repetitive tasks and standardise procedures, thereby achieving process excellence. By automating manual processes, teams are able to liberate valuable time and resources, allowing them to concentrate on higher-value activities, thus enhancing efficiency and productivity.
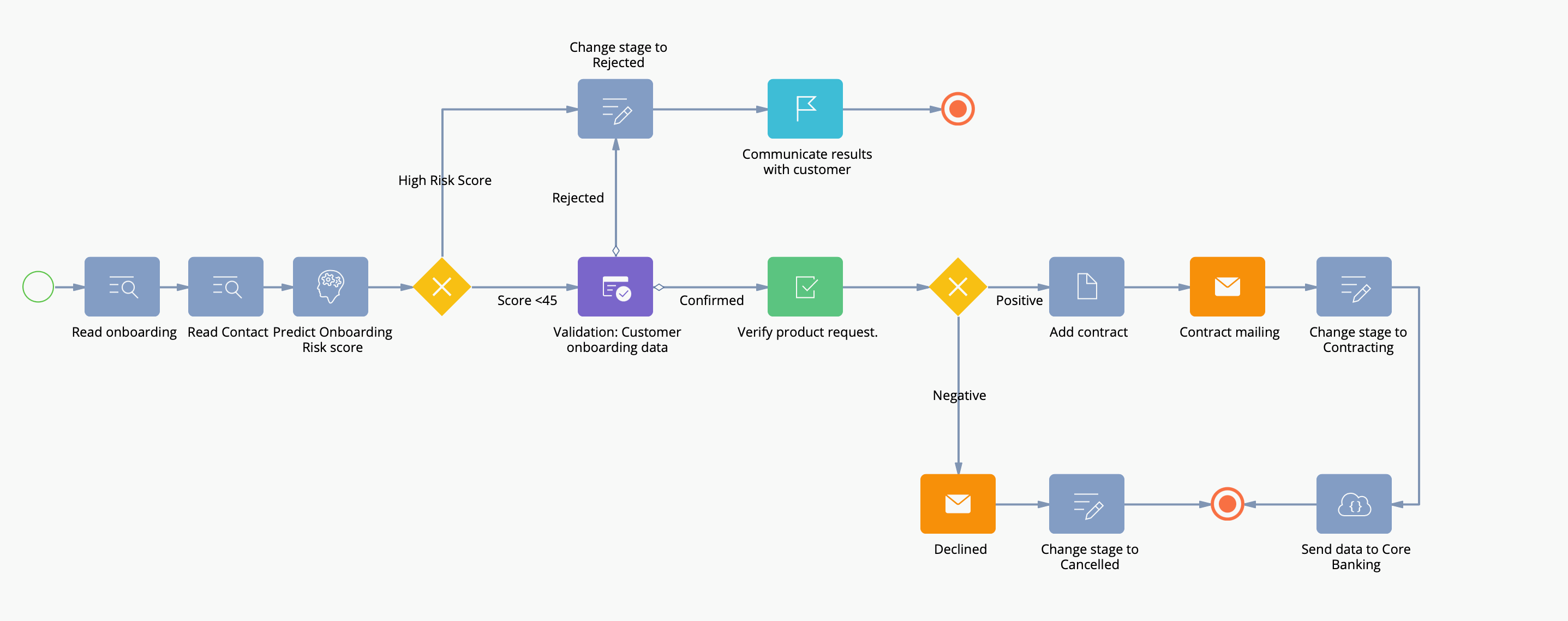
Creatio's formidable analytics and reporting capabilities furnish invaluable insights into process performance, enabling organisations to monitor key metrics, discern trends, and make data-driven decisions to refine their operations. With real-time visibility into process performance, stakeholders are equipped to oversee progress, identify bottlenecks, and promptly address any issues that emerge.
Creatio presents a powerful combination of BPM functionality, automation, analytics, and flexibility, rendering it the quintessential tool for organisations aspiring to elevate their process excellence initiatives. Whether your objective is to streamline workflows, enhance efficiency, or foster innovation, Creatio provides the requisite tools and capabilities to achieve your goals.
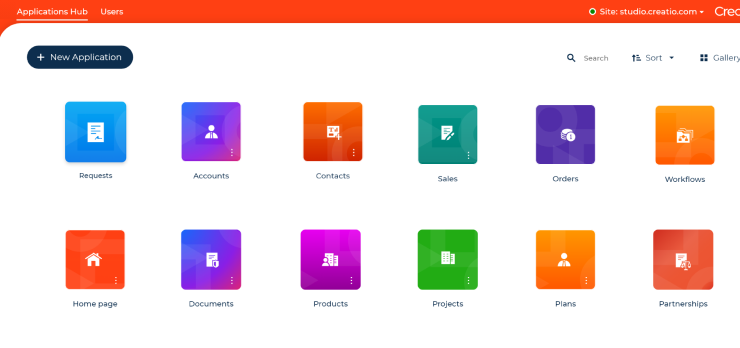
Conclusion
Attaining process excellence is imperative for organisations determined to maintain competitiveness and success in today's ever-evolving business landscape. By concentrating on optimising workflows, eradicating inefficiencies, and cultivating a culture of continuous improvement, organisations can significantly enhance efficiency, elevate quality, and deliver exceptional value to their customers.
Process excellence is not a one-time endeavour but rather an ongoing journey of perpetual improvement and innovation. It necessitates unwavering commitment, astute leadership, and the deployment of the appropriate tools and methodologies to effect meaningful change and sustain long-term success. By embracing the principles of process excellence and harnessing tools such as Creatio's BPM platform, organisations can confidently realise their strategic objectives and secure their place at the forefront of their industry.
FAQ
How to cultivate process excellence?
To cultivate process excellence, adhere to the following steps:
- Establish precise objectives
- Map existing processes
- Identify areas for enhancement
- Define performance metrics
- Engage stakeholders
- Implement best practices
- Design an optimal process
- Implement an optimised process
- Monitor and refine
Is process excellence equivalent to process improvement?
No, process excellence and process improvement are not synonyms, despite their close interrelation. Process improvement pertinent to the enhancement of specific processes. In contrast, process excellence represents a more comprehensive and overarching strategy aimed at attaining and maintaining superior performance across all processes within an organisation.
What are the prerequisites for process excellence?
The requisites for achieving process excellence encompass the following factors:
- Efficiency: Maximising productivity while minimising waste.
- Accuracy: Ensuring precision and correctness in all outputs.
- Quality: Delivering outcomes that meet or surpass established standards.
- Measurability: Implementing clear metrics to evaluate performance.
- Innovation: Introducing creative solutions and novel approaches.
- Agility: Maintaining the ability to swiftly adapt to changing circumstances.
- Flexibility: Allowing for adjustments to accommodate diverse requirements.
- Adaptivity: Evolving in response to emerging trends and challenges.
- Security: Safeguarding data and maintaining operational integrity.
- Compliance: Adhering to relevant regulations, standards, and internal policies.
- Alignment with business strategy and goals: Ensuring processes support organisational objectives.
- Increased customer satisfaction: Enhancing the overall customer experience.
- Reduced costs: Achieving cost efficiencies through improved process management.