What is AI in Manufacturing? Everything You Should Know
While AI is rapidly capturing the attention of business leaders, manufacturing companies must endeavour to catch up swiftly. Implementing AI at a meaningful scale within the manufacturing sector presents a significant challenge, given its inherent diversity and the unique processes found in each factory. This can serve as an impediment when attempting to automate with comprehensive AI tools.
Nevertheless, the global AI in manufacturing market, currently valued at $3.2 billion, is projected to grow 7 times more by 2028. AI holds the potential to revolutionise the manufacturing industry, optimising production processes, enhancing product quality, and reducing downtime and operational costs.
The demand is undeniably present; however, AI solutions must be carefully selected and implemented to foster highly efficient, interconnected, and intelligent manufacturing operations. This article delves into how AI is reshaping the manufacturing market and offers guidance on implementing it for manufacturing optimal efficiency.
What is AI in Manufacturing?
Artificial intelligence (AI) in manufacturing refers to the deployment of advanced systems to automate tasks traditionally undertaken by humans and to optimise manufacturing processes through AI-driven decision-making.
The true power of AI lies in machine learning, deep learning neural networks, and other self-organising systems, which independently learn from available data and experience. Such systems can swiftly identify key patterns in vast datasets, a task that would otherwise be beyond the capability of human analysts.
One well-known application of AI in manufacturing is AI quality control, where machine vision technology enables AI agents to assess product quality, either approving items for shipment or discarding faulty ones. This not only accelerates the evaluation of goods but ensures the reliability of quality assurance checks, thereby streamlining the manufacturing process.
In essence, AI in manufacturing enhances precision, reduces errors, and accelerates production speeds.
Use Cases of AI in Manufacturing
To fully appreciate the value AI brings in manufacturing, let us examine several prominent use cases of smart manufacturing that businesses are increasingly adopting.
Continuous operations
AI facilitates real-time monitoring of equipment data, swiftly identifying any discrepancies in operation. This empowers plant personnel to promptly address issues, thereby preventing downtime and ensuring the consistent quality of the product.
Maintenance assistance
AI serves as a maintenance companion by digitising paper manuals and delivering real-time, step-by-step guidance tailored to the specific issues. This not only streamlines maintenance tasks but also mitigates human error. Furthermore, AI-enabled predictive maintenance ensures equipment health is proactively managed before any problems arise.
Defect detection and inspection
AI-powered visual inspection systems either augment or replace human inspectors, enhancing accuracy and significantly reducing inspection time. These systems analyse data from sources such as vibration sensors, thermal imaging, and oil analysis to assess machinery health, predict downtime, and optimise spare parts provisioning, thereby leading to substantial cost savings.
Moreover, AI insights enable manufacturing engineers to precisely provision spare parts and consumables, forecast downtime, and improve production planning, which in turn reduces maintenance costs and conserves valuable resources.
Supply chain management
Artificial intelligence, powered by machine learning and Big Data analytics, facilitates autonomous planning within supply chains. This continuous, closed-loop, fully automated planning ensures the sustained performance of the supply chain, even amidst volatile conditions. AI applications optimise intricate manufacturing schedules, achieving maximal throughput while simultaneously minimising costs.
For instance, Lenovo has leveraged artificial intelligence to establish a comprehensive supply chain control tower, harmonising all functions – planning, sourcing, making, delivering, and quality control – within a single integrated platform. This Supply Chain Intelligence assists managers in decision-making by simulating various “what-if” scenarios.
Automated quality checks
AI enhances testing and quality control processes by employing image recognition, computer vision, and sensor data to detect equipment malfunctions and product defects autonomously. Additionally, AI analyses production data to discern patterns and propose improvements, thereby reducing the need for rework and decreasing scrap rates.
Cobots
AI powers cobots (collaborative robots), which, in contrast to traditional robots that necessitate isolation from human workers, operate alongside them. These robots perform tasks such as picking parts, operating machinery, and conducting quality inspections. AI-driven machine vision plays a pivotal role in enabling cobots to carry out these functions with efficiency, thereby boosting overall shop floor productivity.
Product design
Generative AI significantly enhances product development by analysing market trends, regulatory shifts, and customer feedback. This enables designers to innovate and customise products with greater precision, ensuring compliance while addressing customer needs. Furthermore, generative AI assists in constructing prototypes and drafting initial concepts that can evolve into fully realised product ideas.
For instance, PIX Moving employs generative design software in Fusion 360, alongside robotics and 3D printing, to decentralise automotive manufacturing. AI-powered generative design optimises chassis development to meet each customer’s unique application and varying physical requirements.
Operational optimisation
AI excels in refining intricate assembly lines by resolving challenges such as worker scheduling, varying production rates, and buffer management. Moreover, it enhances worker productivity and safety by recommending optimal next-best actions and alerting staff to potential hazards.
Automated administration
AI eliminates monotonous administrative tasks by automating processes such as management and approval workflows, effectively acting as a virtual assistant within operational and financial departments, thus reducing human effort and increasing efficiency.
Optimising resource consumption
AI is instrumental in refining energy usage within manufacturing, fostering more sustainable practices. For instance, Doosan Enerbility Steel Mill employs AI to forecast the volume of molten steel required, ensuring efficient energy consumption even when dealing with diverse raw materials.
Digital Twin technology
AI-powered digital twins simulate production cycles to detect potential quality issues or performance discrepancies, thereby enhancing the performance of factory operations.
AI for IT Operations (AIOps)
AIOps utilities big data and machine learning to automate a range of IT operations, including data management, event correlation, performance analysis, and anomaly detection. This automation ensures the seamless operation of IT infrastructure, a crucial component for optimising the functionality of modern manufacturing environments.
6 Advantages of AI in Manufacturing
Enhanced transparency in operations
AI-driven real-time monitoring and data analytics provide workers with greater visibility into production workflows, empowering them to promptly address delays or anomalies.
Furthermore, senior management can continuously oversee operations, making well-informed decisions that optimise overall performance and efficiency.
Safe and efficient production
AI contributes to a safer and more streamlined manufacturing environment by persistently monitoring manufacturing processes.
AI can identify potential hazards, such as equipment malfunctions or unsafe working conditions, and alert workers instantly to prevent accidents. Additionally, AI-powered systems optimise operations by analysing workflows, identifying areas where safety protocols can be reinforced or where inefficiencies might arise, thereby reducing injury risks and enhancing productivity.
Integrating AI with wearable technology allows for tailored safety alerts, further safeguarding employees while driving operational efficiency and reducing downtime.
Enhanced product quality
AI significantly elevates product quality in various ways:
- AI-driven automated quality assurance systems surpass traditional methods in detecting defects and inconsistencies, ensuring each product adheres to rigorous standards before reaching the market.
- Generative design, an AI-powered technique, allows manufacturers to explore myriad design variations, optimising for performance, cost-effectiveness, and material usage.
- AI's capacity to process and analyse vast quantities of customer feedback provides valuable insights into consumer preferences and challenges. This continuous feedback loop ensures products remain of superior quality, aligning with the shifting demands and expectations of the market.
Streamlined innovation
AI facilitates mass customisation by meticulously analysing customer preferences, allowing products to be tailored to specific needs. Additionally, it drives innovation by providing insights into prevailing market trends, ensuring manufacturers stay ahead of the curve.
Increased efficiency
AI enhances production processes by automating mundane tasks, diminishing cycle times, and curtailing waste, resulting in swifter production and more judicious use of resources.
Cost reduction
Through these efficiencies, reduced wastage, and streamlined manufacturing workflows, AI enables manufacturers to achieve substantial reductions in operational costs.
Challenges of Implementing AI in Manufacturing
Whilst the advantages of AI in manufacturing are undeniable, the industry has been notably sluggish in embracing it comprehensively, owing to a series of unique and complex challenges.
The diversity of data in the manufacturing industry
A significant impediment to the widespread adoption of AI lies in the absence of standardised, universal data across the manufacturing industry. Unlike sectors such as finance or retail, where data – such as transaction records or stock market trends – is abundant and easily transferable, manufacturing data tends to be fragmented, often localised and tailored to specific operations or niche domains. This lack of uniformity complicates the development of reliable vertical AI models, as there exists an insufficient quantity of relevant, high-quality data.
Requirements for customisation
The inherent diversity within the manufacturing industry further complicates AI implementation. Whereas more uniform industries may more readily adopt standardised AI solutions, the highly specific nature of manufacturing processes often necessitates bespoke AI applications. This customisation, though essential, is both resource-draining and time-consuming, thus hindering the scalability of AI solutions across various operations or facilities.
The quality and availability of training data
AI algorithms necessitate substantial datasets that are clean, accurate, and well-structured to perform optimally. However, many manufacturers find themselves hampered by the challenge of providing such datasets, often relying on fragmented, inconsistent, or low-quality data.
These deficiencies result in less than optimal AI performance, as the models are hindered in their capacity to learn effectively or make precise predictions. Even when large datasets are available, issues of inconsistency or improper formatting can render them difficult for AI models to process, further complicating the implementation process.
Security vulnerabilities
Manufacturing entities often handle highly sensitive information, encompassing product designs, trade secrets, and proprietary processes. Should this data be compromised, it may lead to the theft of intellectual property, granting competitors an unfair advantage and potentially resulting in considerable financial repercussions. Thus, any AI solution granted access to such sensitive data must ensure adherence to the most stringent security protocols.
AI models themselves are not immune to threats, such as adversarial attacks, where malicious actors manipulate input data to cause AI systems to make incorrect decisions. Safeguarding AI systems against these vulnerabilities is crucial to preserving the integrity of AI-driven manufacturing operations.
Furthermore, manufacturers must navigate a labyrinth of data protection regulations, such as UK GDPR. A failure to adequately secure data could lead to several legal consequences and irreparable damage to a company's reputation.
5 Key Steps for Integrating AI into Manufacturing
To overcome the mentioned-above challenges, it is crucial to adopt a strategic approach when implementing AI within the manufacturing sector. Below are several key recommendations to aid in navigating this complex process:
1. Ensure data quality
AI’s efficacy is fundamentally reliant upon data that is accurate, clean, and consistent. Given that manufacturing use cases tend to be more specific and yield comparatively lower returns than in other industries, the provision of high-quality data becomes even more critical. It is therefore essential to establish robust data management protocols, dedicating time and resources to gathering, cleaning, and organising the data prior to AI implementation, thereby ensuring optimal performance of AI models.
2. Choose the right tools
Rather than embarking upon the labour-intensive task of creating bespoke AI solutions, is it advisable to harness the power of data-centric vertical AI platforms that are specifically tailored to the distinct needs of manufacturing. For instance, automated anomaly detection tools can either augment or entirely replace human workers in quality control, resulting in a more efficient process. Moreover, AI-powered workflow automation tools, such as Creatio, can significantly streamline operational tasks and facilitate administrative processes, thereby driving enhanced productivity.
Given that the manufacturing sector often demands substantial customisation, investing in AI-powered no-code platforms is a prudent choice, as these enable the creation of new LLMs and the automation of manufacturing processes without the requisite coding expertise.
3. Ensure security and compliance
The safeguarding of data is of utmost importance when implementing AI. It is imperative that the AI systems are fortified against potential vulnerabilities and fully compliant with relevant industry regulations. Protecting sensitive information, while ensuring that AI practices align with both legal and ethical standards, is crucial to mitigate any potential risks and penalties.
4. Train your staff
The introduction of AI will inevitably create new roles and demand new skills within your organisation. It is vital to invest in training to ensure your workforce is adept at collaborating with AI systems, with an emphasis on managing and interpreting AI-generated insights. This may necessitate the formation of new teams tasked with overseeing data quality, monitoring automation outcomes, and adjusting to evolving operating models. An organisational redesign may be essential to fully integrate AI into your business structure.
5. Start with targeted experimentation
Initiate AI implementation by focusing on specific, targeted initiatives that allow for swift learning, skill development, and the demonstration of early successes. Concentrate on projects that offer clear ROI potential, this building organisational momentum and securing the support of stakeholders. Such experimentation will be instrumental in determining the most effective applications of AI within your manufacturing processes.
The Future of AI in Manufacturing
The transformative potential of AI in manufacturing is set to reshape the industry.
In the near future, AI will be pivotal in predictive maintenance, continuously monitoring machining processes in real-time. Through the deployment of sensors that gather data on tool wear, acoustic signals, and various machine status indicators, AI algorithms will analyse these inputs to foresee potential malfunction. Such a proactive approach will empower maintenance teams to resolve issues before they result in costly downtime.
Moreover, AI will extend the burgeoning field of additive manufacturing. By integrating advanced sensors, AI will monitor factors affecting materials and fabrication processes, ensuring superior quality and consistency throughout production. This capability will enable manufacturers to compare parts from different production batches, analyse quality assurance data, and identify defects at an early stage, thereby enhancing overall product quality.
Looking further into the future, the prospect of a "factory in a box" may become a reality, wherein AI-powered systems autonomously oversee the majority of the production processes, with human intervention primarily limited to maintenance. These self-correcting machines will not only adapt to wear and tear but will also provide guidance on component replacements, maintaining optimal performance with minimal human oversight.
Beyond the production process, AI will significantly influence the optimisation of factory planning and layout. Through the utilisation of sensors to track and measure potential space and material conflicts, AI can facilitate the design of more efficient and safer factory layouts, particularly in environments characterised by frequent changes or short-run projects.
The implementation of AI in manufacturing will bring a new era of intelligent, adaptable, and highly efficient production processes, driving innovation and productivity across the industry.
Harnessing the Power of AI with Creatio
If implementing AI on a large scale in your manufacturing process seems overwhelming, it is prudent to begin with workflow automation tools that come with pre-configured AI capabilities.
Creatio's no-code, AI-driven platform offers the perfect entry point, enabling the automation of various administrative manufacturing processes such as partner relationships management, quote management, order processing, product lifecycle management, supply chain management, inventory management, and procurement. Furthermore, Creatio's AI ensures compliance by monitoring and enforcing adherence to regulatory standards.
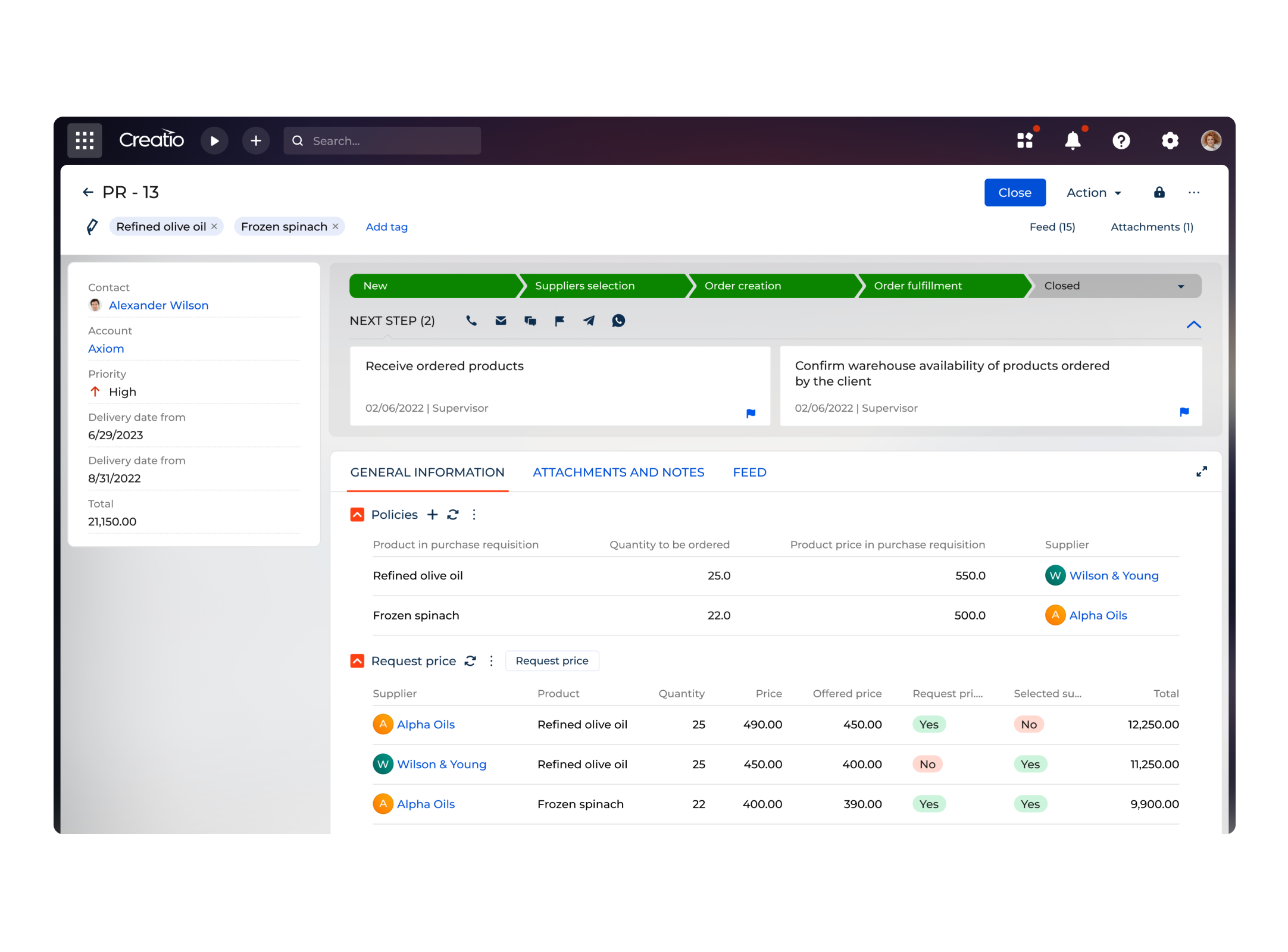
Creatio's dashboard for supply chain management
As a versatile no-code solutions for CRM and workflow automation, Creatio empowers you to develop bespoke business automation solutions by leveraging pre-built components such as trigger actions, data fields, forms, and buttons.
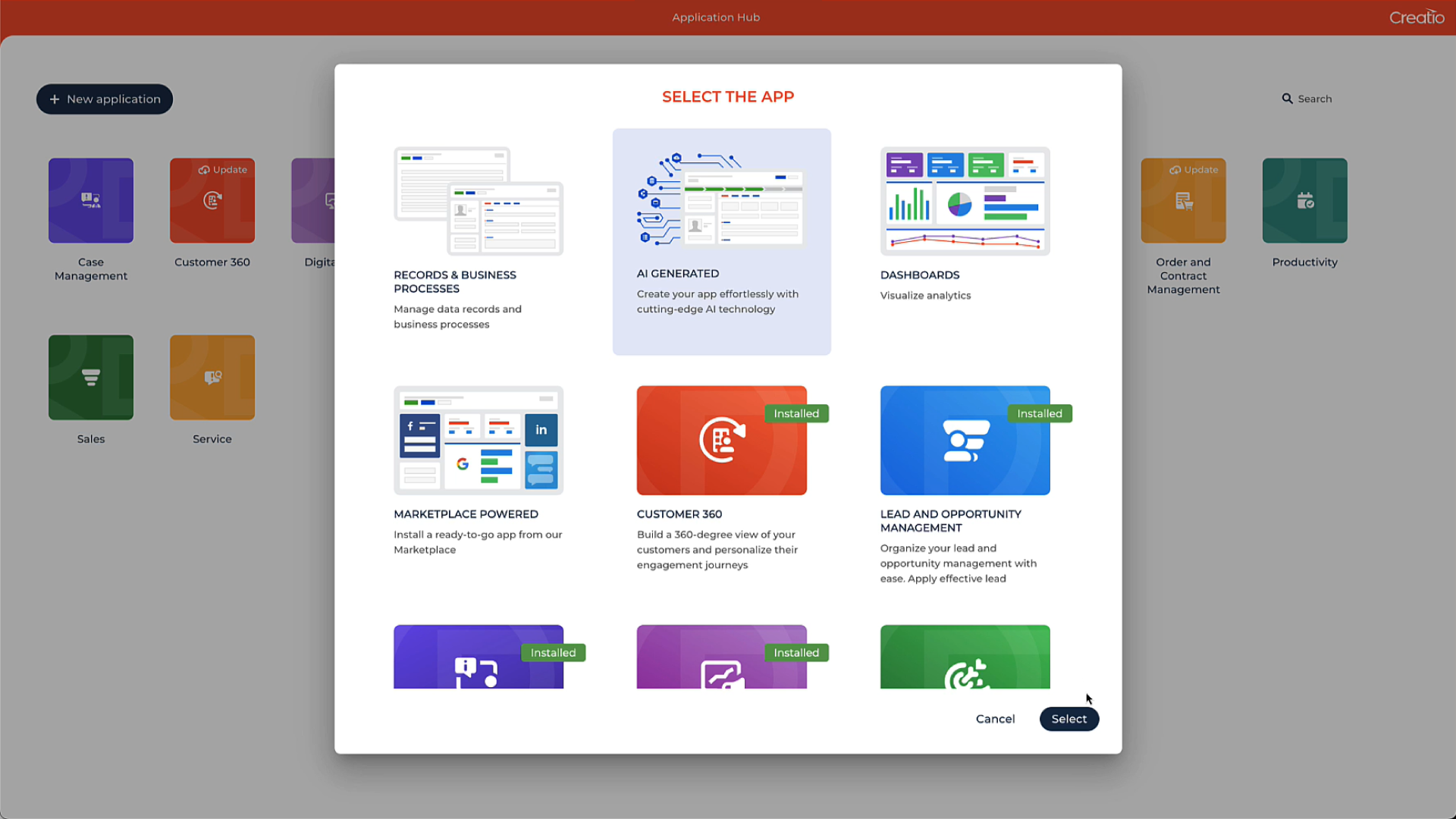
AI-powered app creation in Creatio
This high level of customisation extends seamlessly to Creatio's AI tools, granting you the ability to construct and train machine learning models based on the unique database, thereby ensuring that AI automation is precisely tailored to manufacturing processes while remaining impervious to external disruptions.
Creatio also provides an AI assistant, Creatio Copilot, capable of developing new business applications through natural language commands. For instance, a simple request to Copilot for an application to manage internal audit processes for your financial and legal teams will result in a prototype being generated within mere seconds.
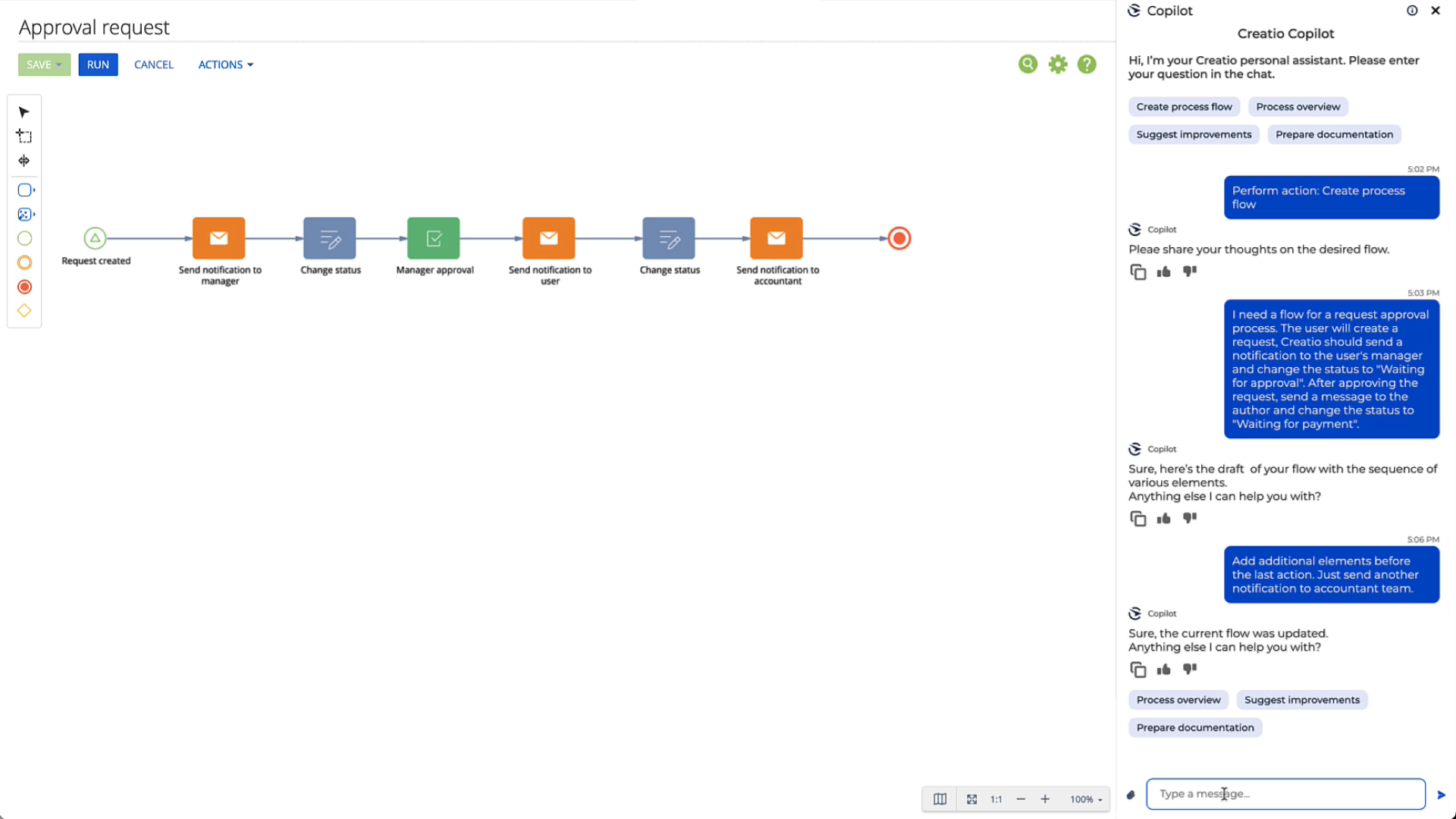
Building an automated workflow with Creatio Copilot
Creatio’s Copilot further enriches customer engagement and fortifies long-term partner relationships by offering highly personalised value propositions. It utilises predictive scoring, AI/ML-driven next-best-offer intelligence, and historical interaction data to deliver bespoke recommendations.
Additionally, Creatio's Marketplace presents a range of connectors with AI tools, designed to optimise administrative processes.
By streamlining and accelerating routine tasks, Creatio liberates valuable resources, enabling your company to foster growth.
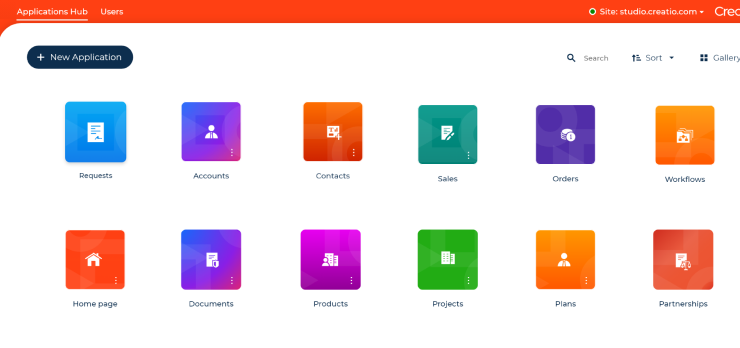
Final Thoughts
In conclusion, the integration of AI in manufacturing should not be viewed as a means of replacing human workers, but rather as a means of augmenting their capabilities. By facilitating seamless collaborations between robots and personnel, AI enables teams to achieve heightened levels of efficiency, precision, and innovation in their endeavours.
As manufacturers increasingly embrace AI-driven solutions, they can anticipate substantial advancements in productivity, quality control, and operational safety. Through the strategic implementation of AI, companies stand not only to optimise processes and reduce costs, but also to unlock new opportunities for growth and development.