-
No-code
Platform
-
Studio
No-code AI-native platform to build applications faster
Discover -
Studio
-
AI-Native CRM
-
Industries
- Customers
-
Partners
-
About
What is Process Excellence? Full Guide
Updated on
August 30, 2024
10 min read
In today's dynamic business landscape, organizations must find ways to gain a competitive edge and improve their performance to stay ahead of the curve. To operate more efficiently, boost productivity, and exceed customer expectations, businesses introduce process excellence.
In this article, we are going to explore the process excellence principles, benefits, and strategies, showing how organizations can leverage this approach to improve their business processes and achieve long-term success.
What is Process Excellence?
Process excellence refers to best practices and tools for business process management and workflow automation that allow organizations to improve the effectiveness and efficiency of their diverse operations. Process excellence involves continuous review of the existing processes within an organization to identify areas for improvement, eliminate bottlenecks, and seamlessly connect multiple business functions.
By embracing process excellence, organizations can streamline operations and boost productivity, which leads to cost reduction, faster time-to-decision, and sustained growth.
What factors determine process excellence?
Process excellence relies on various factors that may differ depending on the nature of the business and its operations.
A process is considered excellent when it meets the following criteria:
- efficiency
- accuracy
- quality
- measurability
- innovation
- agility
- flexibility
- adaptivity
- security
- compliance
An excellent process should also:
- align with business strategy
- improve productivity
- help boost customer satisfaction
- help reduce costs
- help achieve business goals
Using these criteria, businesses can assess whether their processes need improvement to achieve excellence. A process should be optimized until it meets all the criteria outlined above or those specifically chosen by the organization.
Benefits of Business Process Excellence
Striving for process excellence brings numerous benefits to organizations in diverse industries. Here are some key advantages:
- Increased efficiency - streamlining an organization's processes leads to reduced waste, fewer errors, and smoother operations, resulting in higher productivity and efficiency.
- Enhanced productivity - process excellence helps optimize workflows enabling employees to accomplish tasks more quickly and effectively.
- Improved quality - by standardizing procedures and implementing quality control measures, organizations can deliver products and services of greater quality.
- Higher customer satisfaction - process excellence ensures that customer needs are met promptly and accurately, leading to higher satisfaction, and increased loyalty.
- Cost reduction - identifying and eliminating inefficiencies helps organizations save money on resources, labor, and other expenses, improving profitability.
- Faster time-to-market - efficient processes enable organizations to bring products and services to market more quickly, gaining a competitive edge and answering emerging trends and opportunities.
- Enhanced agility - flexible and adaptable processes allow organizations to respond rapidly to changes in market conditions, customer preferences, and regulatory requirements.
- Improved employee experience - involving employees in process excellence initiatives empowers them to contribute to the organization's success, fostering a sense of engagement, and job satisfaction.
- Stronger competitive position - by consistently delivering high-quality products and services, organizations can differentiate themselves from competitors and maintain a strong market position.
- Sustainable growth - process excellence lays the foundation for long-term success by fostering a culture of innovation, and continuous improvement.
Key Steps to Achieve Process Excellence
Achieving process excellence goals requires a systematic approach and a commitment to continuous improvement. Here are the key steps organizations can take to reach this goal:
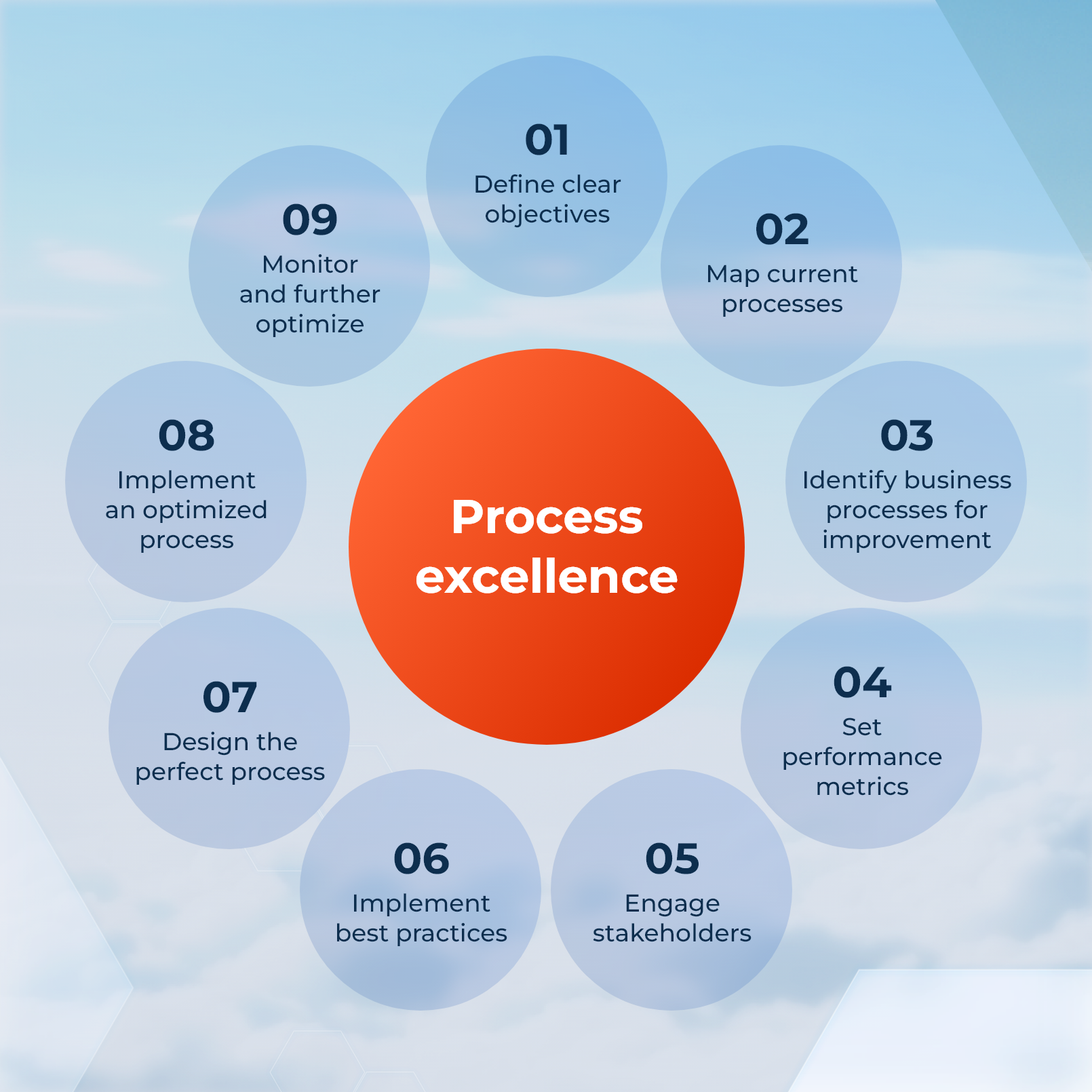
1. Define clear objectives
Start by establishing clear objectives for process excellence efforts and aligning them with the organization's strategic goals and priorities. Remember to select the criteria for process excellence to effectively assess the success of adapting business processes.
2. Map current processes
Conduct a thorough analysis of existing processes to identify the steps, resources, and goals of each of the processes within your organization. Try out process mapping tools that can help you visualize and understand the current state more clearly.
3. Identify business processes for improvement
Identify processes that should and could be improved, and the opportunities to boost efficiency and reduce costs. The goal is to create optimized versions of all the processes that take place within the organization but to succeed, you need to focus on one process at a time.
4. Set performance metrics
Define key performance indicators (KPIs) to measure the effectiveness and efficiency of processes. These metrics should be specific, measurable, achievable, relevant, and time-bound (SMART) to track progress accurately. Make sure you check the primary performance of current processes to be able to compare them after implementing process excellence changes.
5. Engage stakeholders
Involve employees, managers, and other stakeholders in the process of excellence improvements. Encourage open communication, collaboration, and feedback to ensure support from all interested parties.
6. Implement best practices
Research industry best practices and benchmarks to identify strategies for optimizing processes. Implement proven methodologies such as Six Sigma, Total Quality Management (TQM), or Business Process Reengineering (BPR) as needed. We will go over the best process excellence techniques in the next part of this article.
7. Design the perfect process
Designing the perfect process involves creating an optimal workflow that maximizes efficiency, minimizes waste, and delivers high-quality results. This step is crucial for achieving business process excellence as it sets the blueprint for how work will be performed moving forward.
Here's how your organization can approach this stage:
- Visualize the ideal state of the process, taking into account best practices, industry standards, and stakeholder requirements. Document the desired workflow from start to finish.
- Analyze each step of the process to identify opportunities for streamlining and simplification using process mapping techniques. Remove unnecessary tasks, redundancies, and bottlenecks that hinder progress.
- Decide on the best distribution of resources, including personnel, time, and materials, to support the efficient execution of the process. Consider factors such as workload, skill requirements, and resource availability to ensure smooth operations.
- Establish standardized procedures and guidelines for performing each task within the process. Clearly define roles, responsibilities, and decision-making authority to promote consistency and accountability.
- Identify opportunities for automation to streamline repetitive tasks, reduce manual errors, and expedite processing times. Leverage technology solutions such as workflow automation software to automate routine activities.
- Design the process to be flexible and adaptable to changing circumstances, requirements, and priorities.
- Ensure that the designed process complies with relevant regulations, industry standards, and internal policies. Incorporate necessary checks and controls to reduce risks and maintain regulatory compliance throughout the process lifecycle.
- Test out the new process on a limited scale to check its effectiveness and identify any potential issues or areas for improvement before full-scale implementation.
- Document the designed process, including procedures, workflows, roles, and responsibilities.
8. Implement an optimized process
Implement improvements to processes and provide comprehensive training and support to all stakeholders to ensure understanding of the new process, roles, responsibilities, and any updated procedures.
9. Monitor and further optimize
After implementation, continuous monitoring is crucial to constantly evaluate the new organization's processes performance. Use established KPIs to track its effectiveness, identify any areas for improvement, and make necessary adjustments.
Implement a continuous improvement cycle to ensure the process stays in tune with business goals and helps you gain a competitive advantage.
Process Excellence Tools and Techniques
In this section, we explore various tools and techniques that organizations can leverage to achieve process excellence. From Kaizen to 5s methodology, there are numerous approaches available to help companies optimize their processes and streamline operations:
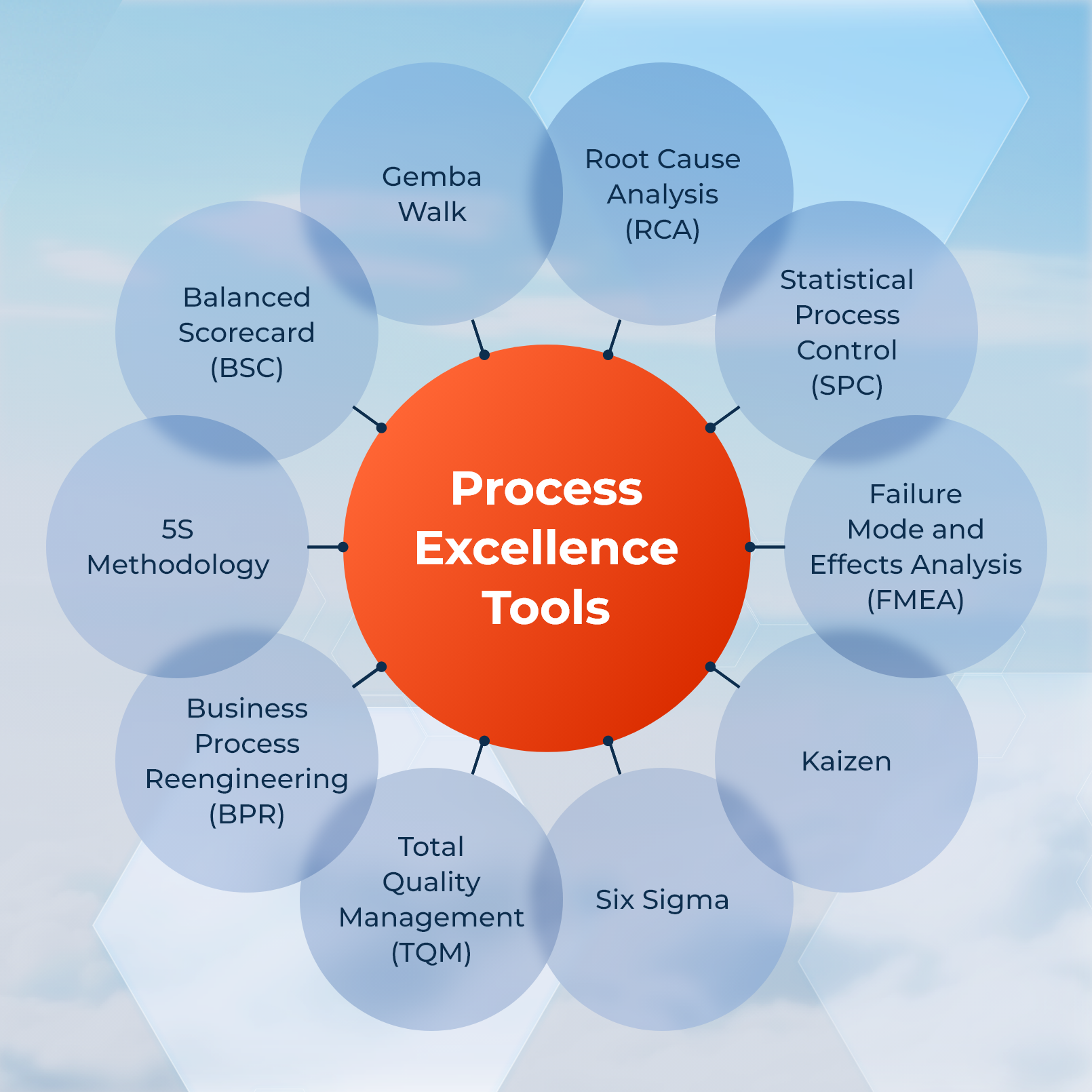
- Root Cause Analysis (RCA) - a problem-solving process excellence technique used to identify the underlying causes of issues or problems within a process. By digging deeper into the root causes of problems, organizations can find practical solutions and address them effectively.
- Statistical Process Control (SPC) - quality control method that uses statistical techniques to monitor and control the stability and performance of a process. It involves collecting and analyzing data over time to detect variations and identify opportunities for process improvement.
- Failure Mode and Effects Analysis (FMEA) - a systematic process excellence approach used to identify and prioritize potential failure within a process, along with its potential effects and causes. It helps organizations reduce risks by addressing potential problems before they occur.
- Kaizen - Kaizen, which means "continuous improvement" in Japanese, is a philosophy and methodology focused on making small, incremental improvements to processes over time. It emphasizes employee involvement, teamwork, and a culture of continuous learning.
- Six Sigma - data-driven methodology used to improve the quality of processes by reducing process variability and imperfections to achieve near-ideal performance. It employs a structured approach, including define, measure, analyze, improve, and control (DMAIC) or define, measure, analyze, design, and verify (DMADV) phases, to identify and eliminate sources of variation.
- Total Quality Management (TQM) - a management approach that focuses on continuous quality improvement across all aspects of an organization. It emphasizes customer satisfaction, employee involvement, and the use of tools and techniques to enhance processes, products, and services.
- Business Process Reengineering (BPR) - involves redesigning and restructuring fundamental business processes to achieve significant improvements in performance, efficiency, and competitiveness. It challenges organizations to rethink and radically redesign processes, often leveraging technology and innovation to achieve breakthrough results.
- 5S Methodology - a workplace organization methodology that originated in Japan and focuses on organizing and maintaining a safe, efficient work environment. The five S's - sort, set in order, shine, standardize, and sustain - help organizations achieve process excellence by eliminating waste, improving productivity, and implementing a mindset of continuous improvement.
- Balanced Scorecard (BSC) - a strategic management framework used to translate an organization's mission and strategy into a comprehensive set of performance metrics across four perspectives: financial, customer, internal processes, and learning and growth.
- Gemba Walk - a lean management practice that involves managers visiting the place where work is done, to observe processes, identify opportunities for improvement, and engage with employees. It promotes direct observation and dialogue at the source to achieve process excellence.
Tips to Achieving Process Excellence
Numerous practical tips can help organizations achieve process excellence. From focusing on customer value to promoting collaboration and communication, we chose 5 tips that offer actionable insights into enhancing efficiency:
1. Focus on customer value
Center your process excellence efforts around delivering consistent value to customers. Understand the needs, preferences, and pain points of your target audience, and tailor processes accordingly to satisfy your customers. Ensure personalized experience and great service to gain customer loyalty.
2. Track and measure results
Track and measure the outcomes of new processes continuously. Monitor key performance indicators, such as cycle time, error rates, customer satisfaction scores, and cost savings, to assess the effectiveness of process improvements.
By keeping a pulse on results, organizations can ensure that process changes deliver the desired outcomes and help them make data-driven decisions to further improve their results.
3. Prioritize continuous improvement
Remember about continuous improvement to ensure business process excellence. Small, incremental changes made regularly will help you enhance processes over time.
Encourage experimentation, learning from failures, and adapting to changing circumstances in your organization to drive ongoing progress.
4. Stay agile
In the fast-paced landscape of modern business, agility is key to success. Embrace flexibility and adaptability in your approach to process excellence. Thanks to that, your organization will be able to swiftly adapt to changing market conditions, keep up with the latest trends in the industry, and respond to emerging opportunities, and evolving customer needs.
5. Invest in process management tools
Invest in a Business Process Management Platform (BPM) to streamline process design, execution, monitoring, and optimization. A BPM platform provides a centralized repository for documenting business processes, capturing data, and automating workflows, facilitating collaboration and visibility across the organization.
With features such as process modeling, workflow automation, analytics, and reporting, a BPM platform enables organizations to standardize processes and improve productivity.
By following these tips, organizations can create a culture of process excellence that enables them to achieve operational efficiency, quality, and customer satisfaction while fostering innovation and constant improvement.
Process Excellence vs. Operational Excellence vs. Business Excellence
In this section, we'll explore the distinctions between Process Excellence (PEX), Operational Excellence (OpEX), and Business Excellence (BEX). While all three concepts share a common goal of achieving organizational success, they have different scopes and approaches:
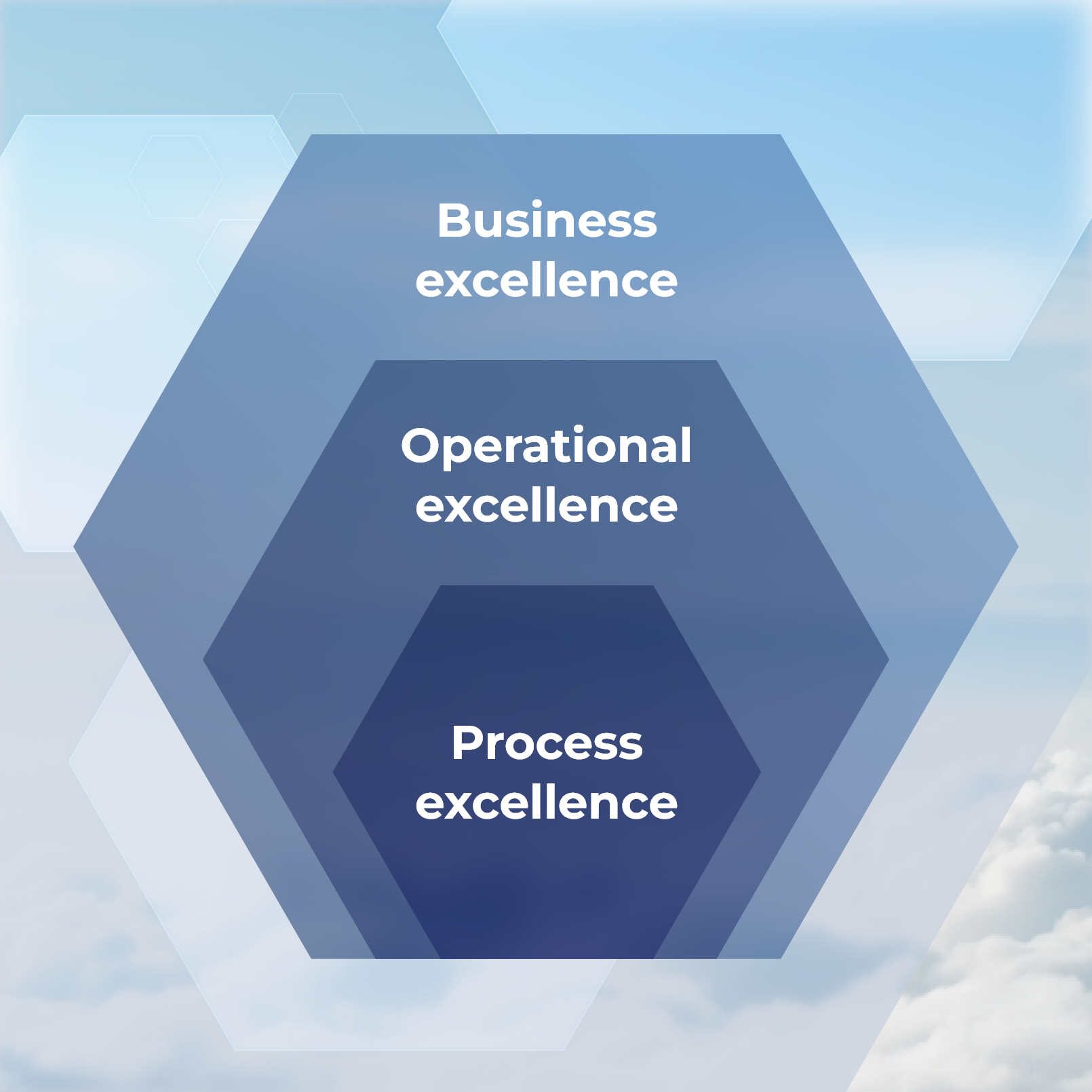
Process Excellence (PEX)
Process Excellence is the systematic approach of identifying, analyzing, and optimizing processes within an organization to enhance efficiency, quality, and overall performance.
It focuses on refining workflows, eliminating waste, and fostering a culture of continuous improvement to drive organizational success.
Operational Excellence (OpEX)
Operational Excellence is a broader concept that encompasses not only process improvement but also the alignment of all aspects of an organization's operations with its strategic objectives. It involves optimizing people, processes, and technology to achieve operational excellence, profitability, and competitive advantage.
Business Excellence (BEX)
Business Excellence is the highest level of organizational performance, encompassing not only operational efficiency but also innovation, and stakeholder satisfaction. BEX goes beyond optimizing processes and operations to focus on holistic business management practices that drive long-term success.
It involves achieving excellence in leadership, strategy, customer focus, workforce engagement, and social responsibility, positioning the organization as a leader in its industry and a role model for others.
Boost Your Process Excellence with Creatio
When it comes to achieving process excellence, having the right tools at your disposal can make all the difference. Creatio stands out as the best BPM platform available, empowering organizations to streamline their operations, and optimize workflows with a maximum degree of freedom, thanks to no-code capabilities and composable architecture.
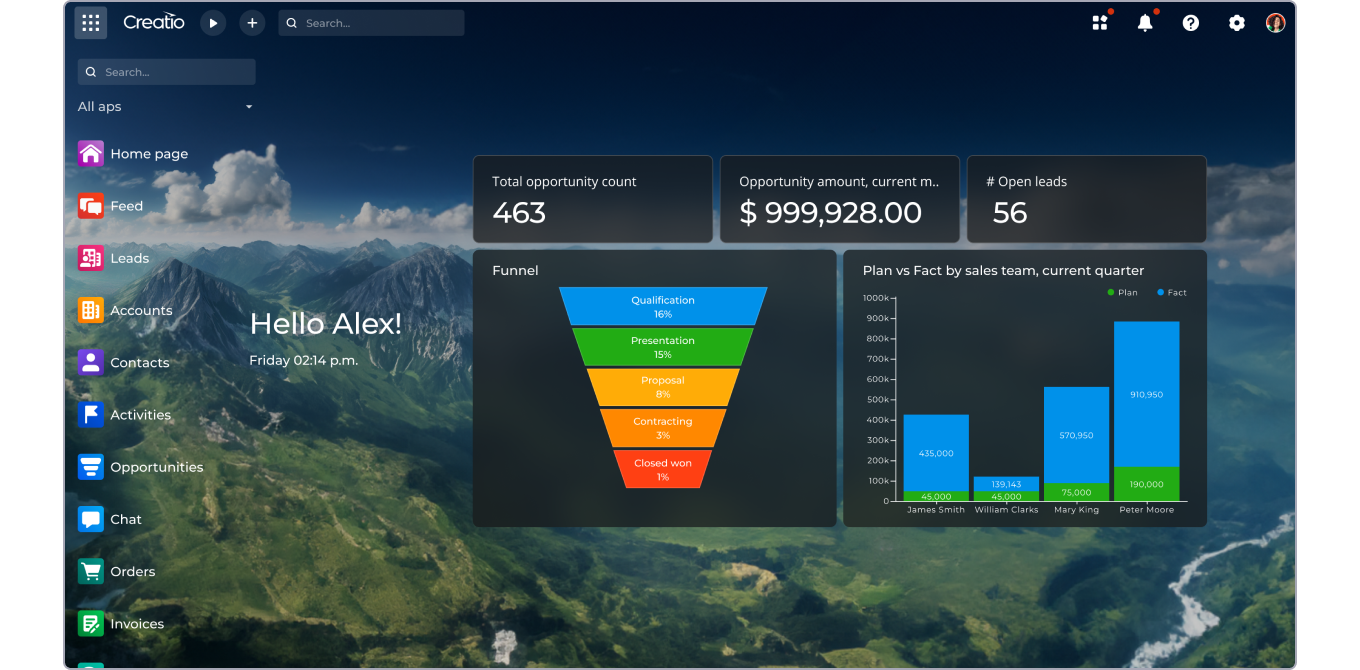
Creatio offers a comprehensive suite of tools and features designed to support every stage of the process lifecycle, from design and automation to monitoring and analysis. Its intuitive process modeling capabilities enable users to visually map out their processes, identify inefficiencies, and design optimized workflows tailored to their specific needs.
With Creatio's business process automation capabilities, organizations can automate repetitive tasks, and standardize procedures, achieving process excellence. By automating manual processes, teams can free up valuable time and resources to focus on higher-value activities, improving efficiency and productivity.
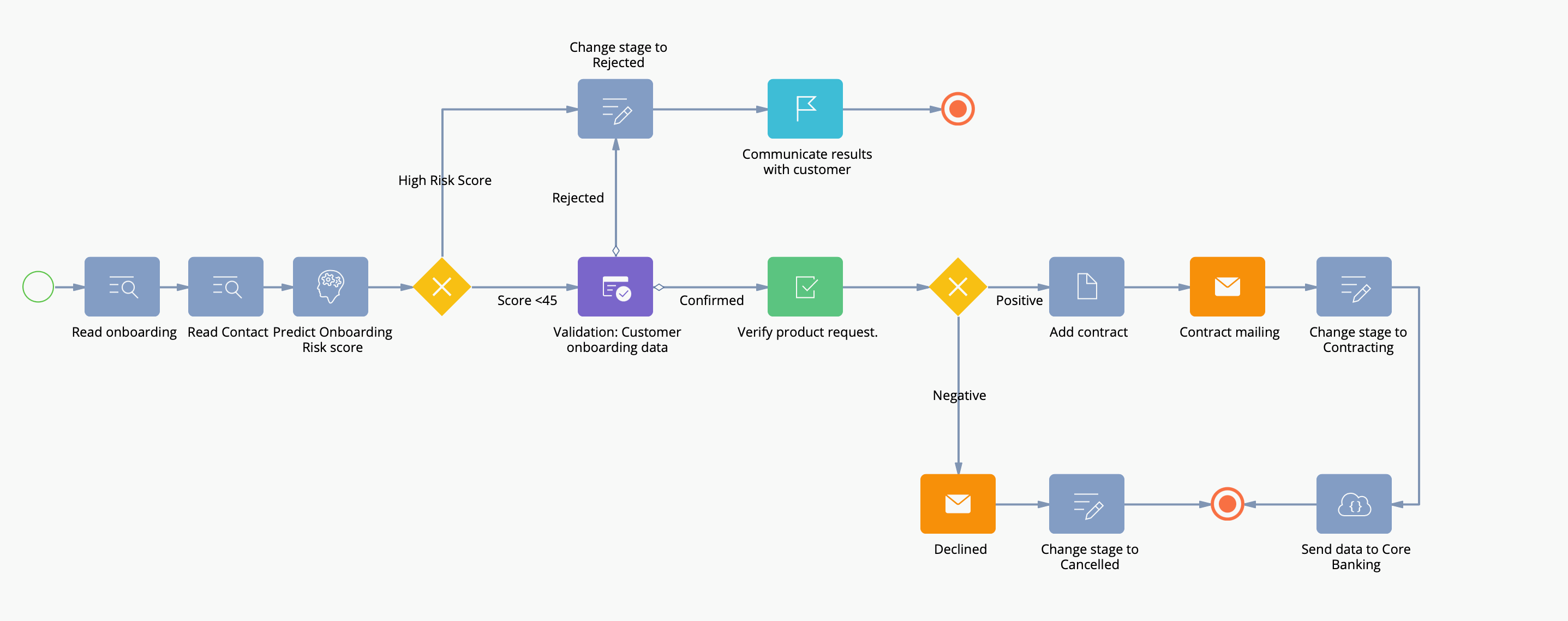
Creatio's robust analytics and reporting capabilities provide valuable insights into process performance, allowing organizations to track key metrics, identify trends, and make data-driven decisions to optimize their operations. With real-time visibility into process performance, stakeholders can monitor progress, identify bottlenecks, and address issues as they arise.
Creatio offers a powerful combination of BPM functionality, automation, analytics, and flexibility, making it the ideal tool for organizations looking to enhance their process excellence initiatives. Whether you're striving to streamline workflows, improve efficiency, or drive innovation, Creatio provides the tools and capabilities you need to achieve your goals.
Start your process excellence with Creatio
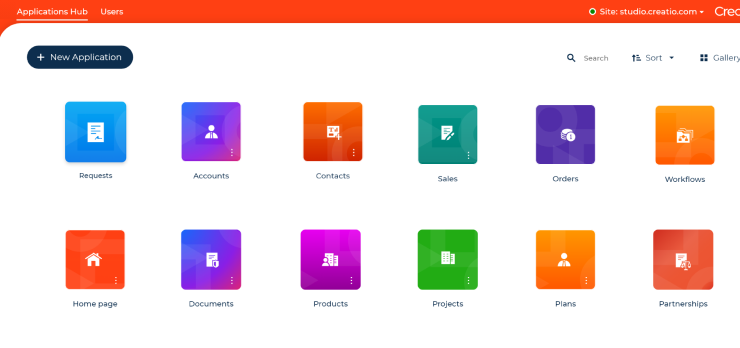
Conclusion
Achieving process excellence is essential for organizations striving to remain competitive and successful in today's dynamic business environment. By focusing on optimizing workflows, eliminating waste, and fostering a culture of continuous improvement, organizations can drive efficiency, enhance quality, and deliver value to customers.
Process excellence is not a one-time endeavor but a journey of continuous improvement and innovation. It requires commitment, leadership, and the right tools and techniques to drive meaningful change and sustain success over the long term. By embracing process excellence principles and leveraging tools such as Creatio's BPM platform, organizations can achieve their strategic objectives with confidence.
FAQ
How do you build process excellence?
To build process excellence follow these steps:
- Define clear objectives
- Map current processes
- Identify processes for improvement
- Set performance metrics
- Engage stakeholders
- Implement best practices
- Design the perfect process
- Implement an optimized process
- Monitor and further optimize
Is process excellence the same as process improvement?
No, process excellence and process improvement are not the same, although they are closely related. Process improvement focuses on enhancing specific processes, while process excellence is a broader strategy for achieving and sustaining high performance across all processes within an organization.
What are the requirements for process excellence?
These factors determine process excellence:
- efficiency
- accuracy
- quality
- measurability
- innovation
- agility
- flexibility
- adaptivity
- security
- compliance
- alignment with business strategy and goals
- increased customer satisfaction
- reduced costs